Many industries use Acumatica. It’s a tool that assists in daily business operations but focuses on finance. Manufacturers are likely using Acumatica but can find it frustrating as it doesn’t pull in the data related to its production. Acumatica and manufacturing can be united, however, with integrations.
How can Acumatica for manufacturing be a game changer? We’ll get to that after explaining more fully what Acumatica is and how Acumatica for manufacturing can help with production operations when integrated with project management software, such as ProjectManager.
What Is Acumatica? 
Acumatica is an online ERP businesses use to help with their day-to-day operations, such as accounting, financial reporting and customer relationship management (CRM). Acumatica is an excellent tool for managing company finances and employees, but it doesn’t have a full suite of project management features that manufacturers can use to help them manage manufacturing operations.
However, Acumatica excels at what it does and is one of the fastest-growing companies in the U.S. It’s a global leader in cloud-based ERP, with over 10,000 customers. It serves a variety of industries, including general businesses, manufacturing, construction, distribution, retail and professional services. It’s so popular because it manages accounting, operations, customers, vendors, employees and other parts of any business’ operations, and it does this successfully by adding efficiencies.
While manufacturers use Acumatica, the professionals that tend to be attracted to the software product are those in finance and accounting, executives, department heads and others who deal with business operations. The software is flexible and has modules that can help with financial management, inventory management, CRM, warehouse management and supply chain management, all of which make Acuamatica for manufacturing a valuable asset.
While there are some project management components to Acumatica, it isn’t built to execute projects and tasks with teams or provide real-time insights. Thankfully, Acumatica for manufacturing can integrate with other software that fills in those holes.
How to Use Acumatica for Managing Manufacturing Operations
Acumatica for manufacturing is a good fit up to a point. It can drive efficiency and develop future-proof agility through real-time insights for every department, access to that data anytime, anywhere and end-to-end control over production. There’s also support for multiple manufacturing methodologies and automated order management and streamlined procurement.
That covers many bases but leaves managing manufacturing operations out of the mix. With integration, that hole is filled and Acumatica for manufacturing lives up to its promise to serve all the needs of its manufacturing clients.
ProjectManager is award-winning project and portfolio management software that Acumatica has recognized as its office project management application. The project management software has met Acumatica’s high standards for integration and functionality. When Acumatica users integrate ProjectManager, they get a bi-directional project management application that empowers them to seamlessly synchronize project data, automate financial tasks and optimize workflow processes, making Acumatica for manufacturing all they need to manage their production processes. Contact ProjectManager to learn more.
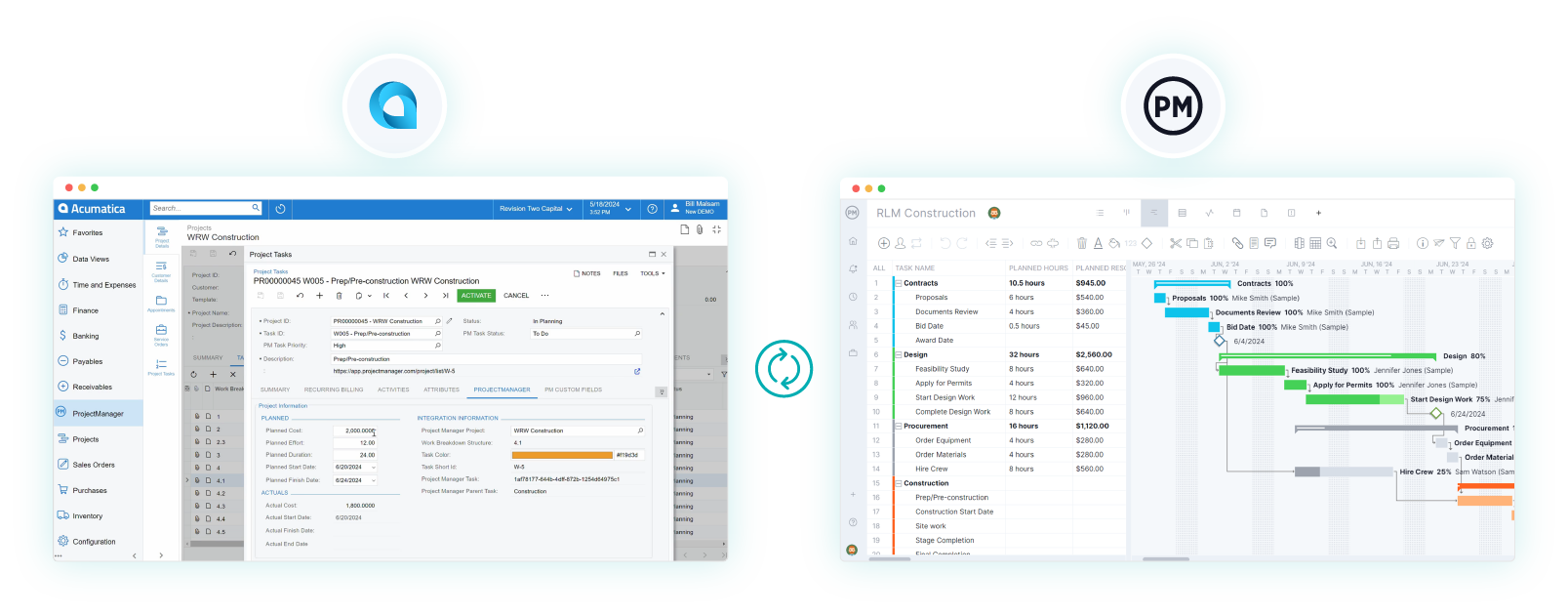
Acumatica Manufacturing Module Features
With ProjectManager’s Acumatica integration, manufacturers cover all the bases. That’s because Acumatica manufacturing modules help manage every other aspect of a manufacturing business all in one place. These Acumatica manufacturing modules boost efficiency and meet manufacturing needs.
Production Management
The ERP offers flexibility to manage production in make-to-stock, make-to-order, engineer-to-order, configure-to-order, project-centric, job shop, batch and repetitive manufacturing environments. Provides insights into production orders, work-in-progress and job costs. Creates production orders from sales orders, monitors and manages performance and schedules and pre-assigns lot and serial numbers.
Inventory Management
Acumatica’s inventory management helps simplify the inventory process with item management, quality traceability and replenishment to balance supply and demand. It offers kitting and disassembly and flexible locations by warehouse, aisle, rack, shelf and bin.
Bill of Materials and Production Routing
With this Acumatica manufacturing module, users can create, maintain and control master data definition of products and processes. It helps to improve scheduling, costs and material planning with accurate and well-defined bill of materials. There’s also an integrated manufacturing bill of materials and routing, multiple cost methods and capabilities, plus a multi-level bill of materials and routing.
Material Requirements Planning (MRP)
Use this Acumatica manufacturing model to satisfy customer requirements while maintaining optimal inventory levels. It helps to synchronize material requirements with production schedules. Use this to improve profiles and maximize utilization.
Manufacturing Estimates
Create manufacturing estimates, control costs and markup for fixed and variable cost elements. It also integrates quotes with embedded customer relationship management (CRM). With this Acumatica manufacturing module, manufacturers can boost sales with fast and accurate estimates.
Sales & Purchase Order Management
This order processing software module from Acumatica manufacturing centralizes sales activity, from quote entry and order fulfillment to shipment creation, pricing, discounting and stock status inquiries. It benefits manufacturers with integrated workflow and cross-company transactions.
Project Management Integration for Acumatica by ProjectManager
Acumatica is very thorough in managing many manufacturing operations, but planning and scheduling manufacturing projects requires proper project management software. That’s where the ProjectManager integration comes in. ProjectManager also is a collaborative platform. Team collaboration is nearly impossible in Acumatica. However, with the ProjectManager integration with Acumatica, manufacturers are connected whether in the office, factory floor or warehouse.
For more information on this integration and a demo, watch the quick 10-minute video below.
What Is ProjectManager?
ProjectManager is software for business excellence. It helps plan projects, build workflows and manage resources with powerful features that the whole team can use. The cloud-based software has multiple project views that production managers and employees in all departments can use to work together.
Founded in New Zealand in 2008 and moving to the United States in 2014, the company won a Project Management Institute (PMI) award in 2009 and won two awards from Deloitte in 2013. In 2019, it was recognized by Inc. in its 5,000 list of the fastest-growing companies in the United States as well as the Fast50 list of fastest-growing companies in Austin, Texas.
Why Use ProjectManager for Managing Manufacturing Projects?
ProjectManager is manufacturing project management software that manages projects, processes and teams online. It helps manufacturing teams manage orders, track production cycles and plan complex, time-sensitive projects on one flexible platform. Its powerful, but easy-to-use project management tools help manufacturers scale without getting lost in the details.
There are features to plan and mitigate bottlenecks and waste, set milestones, link dependencies and identify the critical path for better execution. With unlimited file storage, manufacturers can place all their orders, documents and related notes in one, easily accessible place. Then track fulfillment cycles from start to finish and deliver updates to customers. It’s fast and simple to generate reports on cost, time and resources for tasks, projects and portfolios to identify areas of improvement and analyze margins.

Benefits of Acumatica Project Management Integration
Acumatica isn’t a project management software. While it has many modules that can help with manufacturing, it’s only with ProjectManager’s integration that it offers a full-service solution. Integrating ProjectManager with Acumatica connects the business operations team with the production team allowing each to work in their preferred software and still transfer data seamlessly from one software to another.
Not only does this create faster delivery, better data accuracy and a more effective workforce, but ProjectManager can create detailed project plans that track progress, allocate resources and monitor the financial impact of Acumatica’s ERP solution. Key benefits include real-time data synchronization, such as plans, resource schedules and task management. Data accuracy is improved by di-directional integration.
Manufacturers can automate workflows, which streamlines cost and resource management processes, as well as create customized workflows to fit specific business needs. With ProjectManager’s integration users can collaborate and gain visibility into team progress, workload and more. This provides greater insights into plans, while project accounting and reporting are updated in real time so financial teams get a fuller picture that leads to better management, forecasting and outcomes.

Contact ProjectManager to Learn More
Take Acumatica for manufacturing to the next level by integrating with ProjectManager. Request a demo or ask a question.
Why ProjectManager Is the Best Acumatica Integration for Manufacturing Project Management
For manufacturers looking for the best project management integration, ProjectManager has greater scope and features than any other candidate in the Acumatica marketplace. ProjectManager is award-winning project and portfolio management software that manufacturers can use to manage their projects, gain key portfolio insights, reduce data gaps and better understand the financial impact of projects. Use ProjectManager to schedule, monitor, manage resources, track costs and workload.
Make Project Schedules and Monitor Progress
Production managers can make detailed production schedules on Gantt charts or the sheet page, which is just like a Gantt chart, but without the timeline. They can link all four types of task dependencies to avoid costly delays and filter for the critical path to identify essential tasks. Then set a baseline and monitor planned progress against actual progress in real time to help stay on track.

Manage Resources and Track Costs
Resources can be planned on the Gantt chart or sheet view, including associated costs. When onboarding teams, availability can be set, including vacation time, PTO and global holidays, which streamlines assignments. Toggle to the real-time project or portfolio dashboard to get a high-level view of costs and more on easy-to-read graphs and charts.

Balance Team Workload
Keeping the team’s workload balanced allows each to work at capacity without burnout, which makes them more productive. Managers can view resource allocation on the color-coded workload page or the team page, which collects everyone’s assignments. From there, managers can reallocate resources as needed to balance the team’s workload.

Free Manufacturing Templates for Excel
For those not ready to upgrade to ProjectManager’s integration with Acumatica for manufacturing, there are over 100 free templates available on our site for immediate download. There are free project management templates for Excel and Word that help with every aspect of managing a project across many industries. The following are some that can improve the manufacturing process.
Production Schedule Template
Use this free production schedule template for Excel to balance supply and demand when producing commodities. Track the production of the product over a period and get the flexibility necessary to respond to fluctuations in supply and demand.
Inventory Template
Managing inventory requires the recording of inventory levels and the tracking of inventory turnover. This free inventory template for Excel shows what’s in stock and tacks those materials to better understand inventory turnover.
Bill of Materials Template
Manufacturers use this free bill of materials template for Excel to plan the materials needed for production. It helps with estimating, planning and inventory control, as well as safeguarding against production delays and waste.
Capacity Planning Template
Capacity planning is used to figure out how much production capacity is needed to meet demand. Using this free capacity planning template for Excel allows managers to list tasks, their estimated duration, allocated resources and the hourly rate for each resource.
Related Manufacturing Content
Acumatica for manufacturing with ProjectManager integration is a partnership that delivers on the successful completion of projects. For those who want to know more about the manufacturing process, production planning and capacity, below is a sampling of the weekly blogs published on the site that relate to manufacturing.
- Acumatica Construction Edition
- Acumatica for Project Management
- 14 Free Manufacturing Excel Templates
- Manufacturing Operations Management Explained
- Production Planning 101: Making a Production Plan (Example Included)
- Production Control: Process, Types and Best Practices
- How to Calculate Production Capacity: Formula & Examples
ProjectManager is online project and portfolio management software that connects teams whether they’re in the office, on the factory floor or in the warehouse. They can share files, comment at the task level and stay up to date with email and in-app notifications. Join teams at Avis, Nestle and Siemens who use our software to deliver successful projects. Get started with ProjectManager today for free.