All businesses have assets, and if you want to stay in business, you need to know what those assets are. To start, you have to do an equipment inventory and make an equipment inventory list. That’s not as easy as it might sound.
There are many items to track in your equipment inventory. Of course, you must start by making an equipment inventory list. However, we’ll begin by defining what an equipment inventory is and show you how to make an equipment inventory list, including a free equipment inventory template.
What Is an Equipment Inventory?
Equipment inventory is everything that a company has in its possession. This can vary across companies and even across departments. For example, an IT team will have an equipment inventory that includes such assets as desktop computers, laptops, printers, scanners, POS systems, computer accessories, software applications, etc.
Manufacturers will have an equipment list that’ll include goods and materials as well as machinery. Construction companies will likely have heavy machinery unless it’s rented, as well as tools and other trade items. Regardless of what the assets consist of, they should be listed in detail and itemized.
Having an equipment inventory is key to having more control over our business assets. In turn, having a full equipment inventory becomes an asset for the company. It provides a buffer between department requirements and order fulfillment. Using project management software helps you keep track of your equipment inventory.
ProjectManager is online project management software that gives you a central hub for your equipment inventory and the ability to track it in real time. Collect your equipment inventory on our list view and generate reports on your equipment inventory to know when you need to resupply. Get started with ProjectManager today for free.
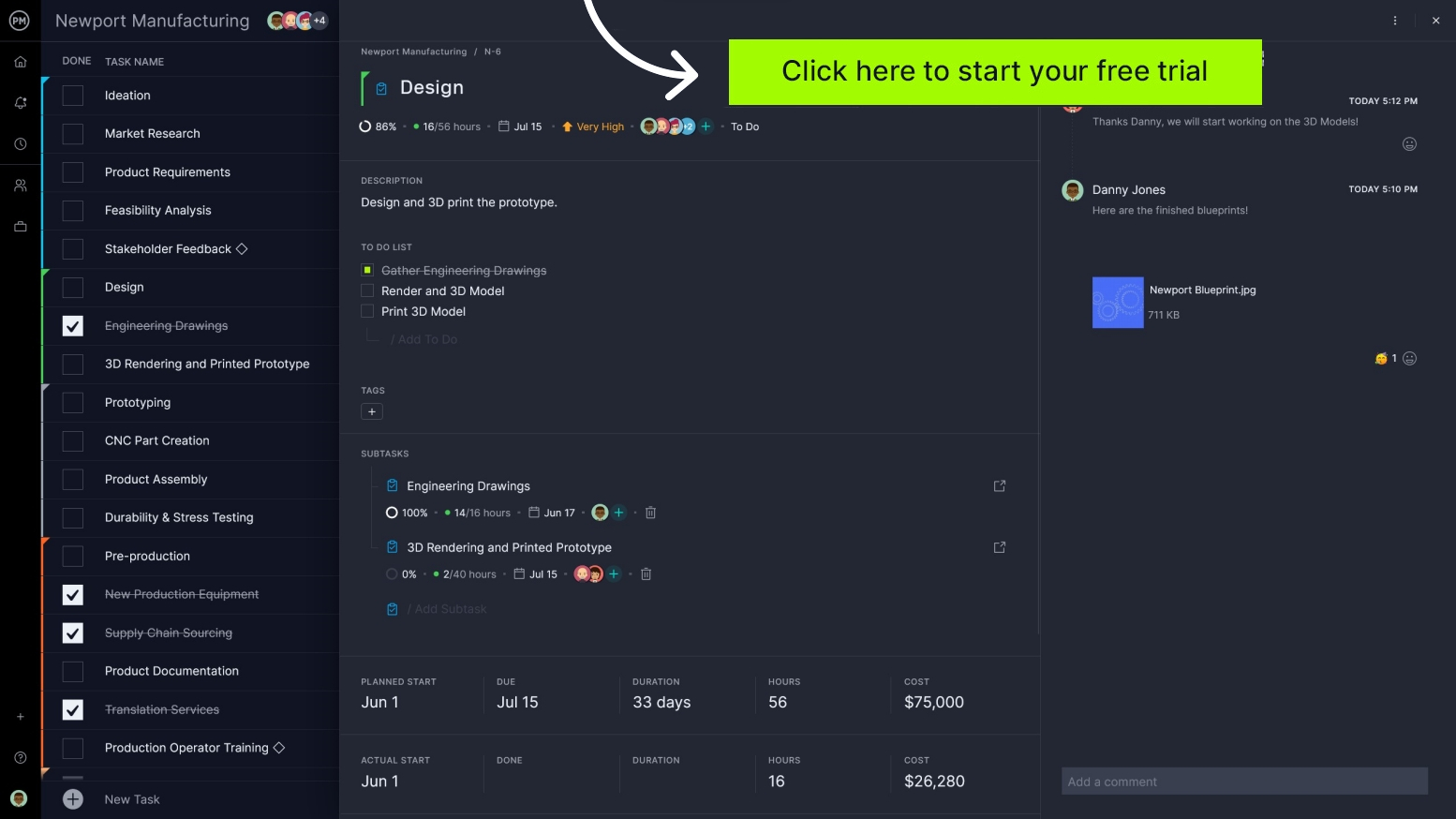
What Is an Equipment Inventory List?
An equipment inventory list is a full overview of the assets of an organization. It’s essential for auditing and insurance policies and is helpful when deciding whether you need to resupply or buy new equipment.
Having an equipment inventory list is key to proper management. It can be made in any number of spreadsheets, from Excel to Google Sheets or Numbers, but there are software solutions that provide you with more functionality than a static spreadsheet offers.
If you don’t have a tool to make an equipment inventory list, consider creating one right away. It’s not a difficult procedure, but it should be thorough.
How to Create an Equipment Inventory List
In order to have a thorough and useful equipment inventory list, you need to set up a system to consistently inventory your assets. That’s a lot of work upfront but it pays off to have the equipment inventory list updated and accurate.
You’ll want to start by knowing exactly what you have, including make and model, etc., how and where the assets are being used and how to best use the equipment inventory. That includes what you need and what you can do to get more life out of your equipment inventory.
Again, this equipment inventory list should have all your assets. Use your team members as resources to make sure you’re covering everything. The list, as you see, must be detailed. But don’t think of this as one-and-done; you’ll need to review and revise as the equipment is damaged, repaired and replaced.
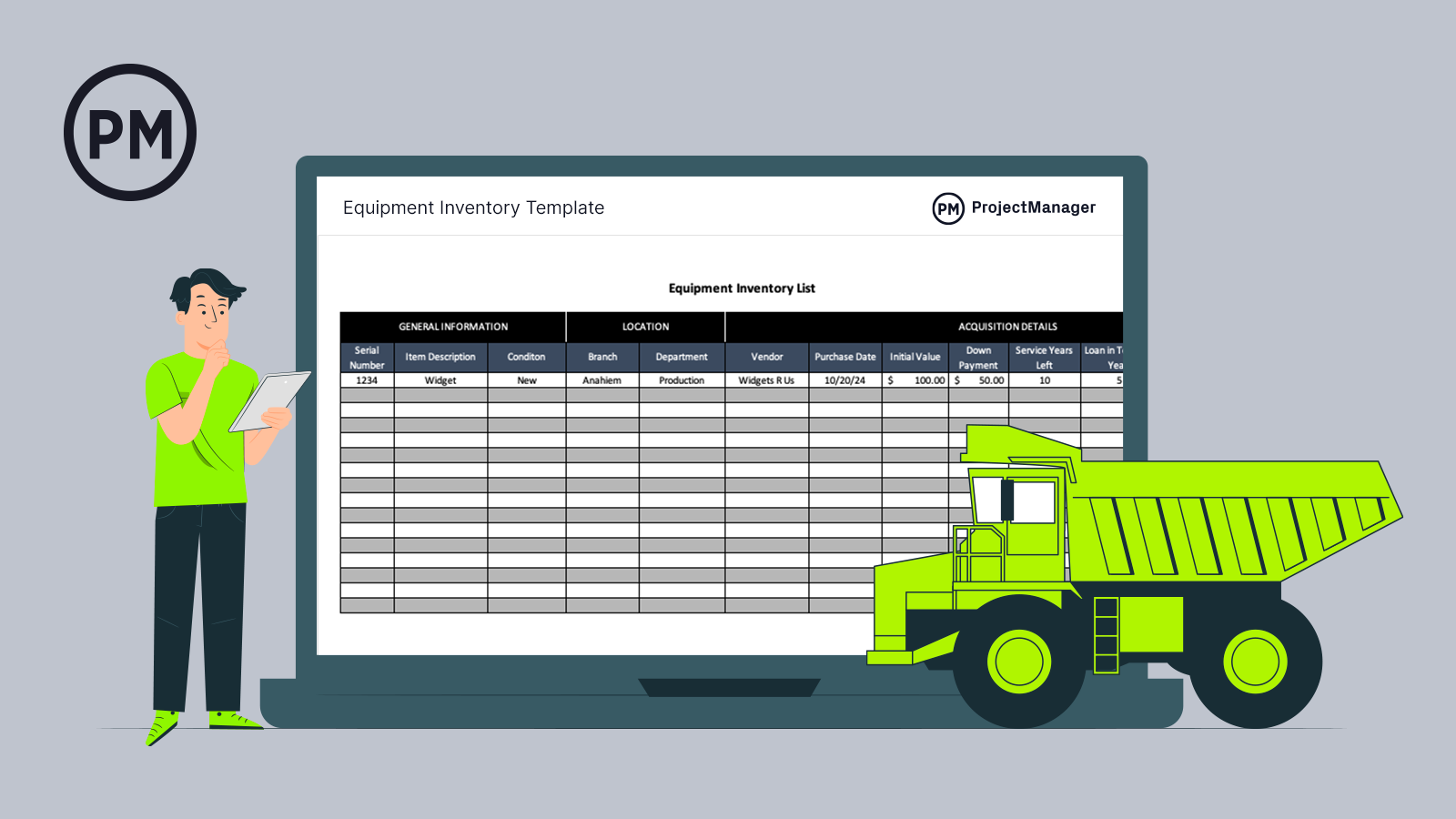
Get your free
Equipment Inventory Template
Use this free Equipment Inventory Template for Excel to manage your projects better.
1. Gather General Information About Your Equipment
To begin, start collecting general information about your equipment. This process is led by the office or equipment manager and other staff will help update it. This process should be structured to ensure that new equipment is added and any changes to the equipment are recorded.
It’s a good idea to begin the equipment inventory list by breaking it into categories. Each category has subtabs to collect the details about the equipment. The following details are part of any thorough equipment inventory list.
- Item serial number: This is the unique equipment number, tracking number or PIN depending on the type of equipment that’s being listed. These numbers are important to track any updates or recalls or to identify the equipment if recovered after theft.
- Item description: This is where you note the make or model of the equipment. You should also describe its color, any markings and other details. All of this helps if the equipment is stolen and you have to fill out an insurance claim.
- Condition: Note the status of the equipment, such as whether it’s new, in good condition, needs repairs and so forth. This crucial information helps you know when to reorder a specific item or repair a piece of equipment.
2. Indicate the Location of Your Equipment
Another aspect of the equipment inventory list is where those assets are. Smaller businesses might not find this as useful as global corporations, but regardless of the size of your company, location is important. You need to find the asset if you want to use it, repair it, decommission it, etc. That means what drawer it’s in or which satellite office.
- Branch: For companies that have branch locations, you’ll need to detail in which branch the asset is. This is especially helpful, again, if the piece is stolen as it zeroes in on a target radius where the piece is most likely to be found.
- Department: As noted, even if your business is under one roof, you’ll still want to detail the location of the asset so it’s easier to track its condition.
3. List Equipment Acquisition Details
The purchase management information related to each piece of equipment is also important when compiling an equipment inventory list. These details will help track the loan if these purchases are on credit, but also the longevity of the item and when you’ll need to repair or replace it. The following are some of the items you can identify and add to your equipment acquisition list.
- Vendor: This is where you bought the item, whether it’s a vendor, company, store, etc. This is important so that you know where to go if that piece of equipment has to be replaced.
- Purchase date: Knowing when you bought the asset is helpful to forecast how much longer you can expect it to be useful. That is the life cycle of the equipment. Of course, this is also necessary if filing a police report or insurance claim.
- Initial value: The cost of the equipment determines how you care for it. All equipment is valuable and shouldn’t be neglected, but if the piece is expensive it might require extra security.
- Down payment: What’s the amount you put down when buying the equipment on credit? This is important as you’ll be paying off the equipment over a period of time and the value of the item speaks to how and when you repair or replace it.
- Service years left: This notes how much time the equipment is valuable to your business and that your team members can use it safely.
- Loan term in years: If you didn’t lease the equipment but took out a loan to buy it, this captures the number of years you have fixed with your bank to repay the loan for the equipment.
- Loan rate: This is where you write down the interest rate as it’s applied to your bank loan.
- Expected value at end of the loan term: Once you’ve paid off your loan, if the equipment is still useable, you’ll want to figure out how much longer it’ll be viable. Most equipment loses value over time, so you’ll want to calculate the expected value (EV) for each piece of equipment when it’s paid off.
4. Measure Monthly Costs
This is where you calculate the amount of money you have to pay each month for the equipment. This knowledge is important to making decisions such as if repairs are worth the effort on a piece of equipment that’s already on its last legs. You can conduct a quick cost-benefit analysis to better assess the situation.
- Monthly operating costs: Determining operating costs means knowing the cost of owning or renting the equipment plus the cost of maintaining it plus the cost of running it, such as fuel, electricity, etc.
- Monthly payment: This is what you have to pay each month for one piece of equipment, whether that’s a lease or a loan.
5. Gather Depecriation Information
Another thing to track is depreciation. In other words, the reduction in the value of the equipment over time that’s due to the wear and tear of use. The following allows you to chart this.
- Current value: Simply put, that’s how much the piece of equipment is worth right now. In other words, it’s the original price of the item with the depreciated value from age, wear and tear subtracted from it.
- Annual straight-line depreciation: This is a method to figure out how much equipment will depreciate over its life cycle. The idea behind this is that a piece of equipment depreciates uniformly over a period of time until it’s no longer of value and will be salvaged.
- Monthly straight-line depreciation: Same as annual straight-line depreciation, but over a shorter period of just a month.
Free Equipment Inventory Template
That’s a lot of data to collect for each piece of equipment. You then multiply that by the assets in a business for an idea of how time-consuming this process is. Using an equipment inventory list template is one way to streamline the effort. The document has the various aspects of an equipment list outlined, and all you have to do is fill in the blanks. Download our free equipment inventory template to get started.
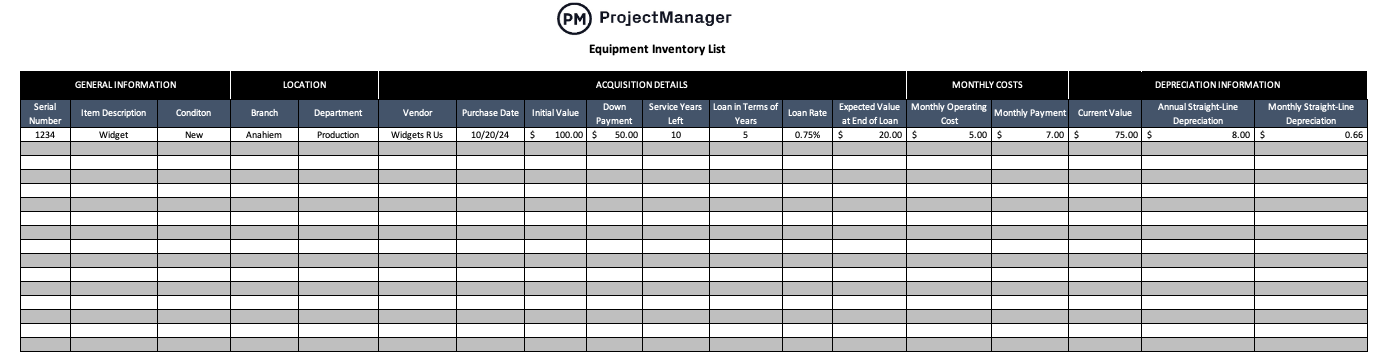
Benefits of Equipment Inventory Lists
After reading this far, you might throw your hands up and say, this process takes too much time, it’s not worth it. While it’s a lot of work, the benefits far outweigh the effort. For one, you’ll make better business decisions once you’ve gathered this critical knowledge of your assets. It helps inform your resource management.
Equipment is expensive. Having an equipment inventory list is one way to understand those costs. This informs you of buying and maintenance routines. The equipment inventory list is especially helpful for preventative maintenance. You can get more out of your assets and better track maintenance.
It’s not only resource management but creating budgets that are bolstered by equipment inventory lists. You can budget for upcoming purchases and maintenance more accurately, which means keeping that machinery online and avoiding disruption in your production. That increases efficiency and while holding your team members accountable by knowing who has what equipment.
ProjectManager & Equipment Inventories
We’ve pushed our free equipment inventory list template as an entry point into having more control over your assets, but templates are static documents and equipment inventory is anything but static. ProjectManager is online software that helps you keep track of resources in real time. Now you have the tools you need to know when it’s time for maintenance or to replace old equipment without causing any delays in your production.
Manage Resources on Interactive Gantt Charts
There’s a ton of data related to equipment inventory. With our Gantt charts, you can track the costs and resources related to your production either over a project or multiple projects with the roadmap feature. Just toggle over from the list view on which you created your equipment inventory list onto the Gantt chart. Now you can track financials, due dates and more. Once you have your plan completed, set a baseline to capture that data. Now you can track the planned versus the actual effort in real time and always know the current state of your resources.

Track Resources with Real-Time Dashboard
Once you set a baseline, you can track your resources across all the features of our software. Whenever you want a high-level view of your inventory, use the real-time dashboard to track six metrics, including cost. There’s no setup required as with other lightweight tools that make you configure the dashboard. Our dashboard is born ready when you are.

When you need more data, use our one-click reporting features. You can create reports on your team’s workload, costs, status and portfolio status, plus more. Each report can be customized to show only the information you’re interested in and then easily shared with stakeholders. Now you have control over your inventory, it doesn’t have control over you.
ProjectManager is award-winning software that helps you manage and track your equipment inventory in real time. Our collaborative platform makes it easy for every department to update their equipment inventory lists in real time, share files and comment. Get started with ProjectManager today for free.