We all want to improve, or we should. Complacency might feel good in the moment, but that moment quickly passes. Don’t be left behind. The question is how can one improve? There are many answers, from educational and physical fitness to spirituality. But is there a unifying theory of improvement, and if so, can it be sustained?
Have you heard of kaizen? It’s a Japanese word that literally means improvement. That feels like a good place to start on our quest towards improvement.
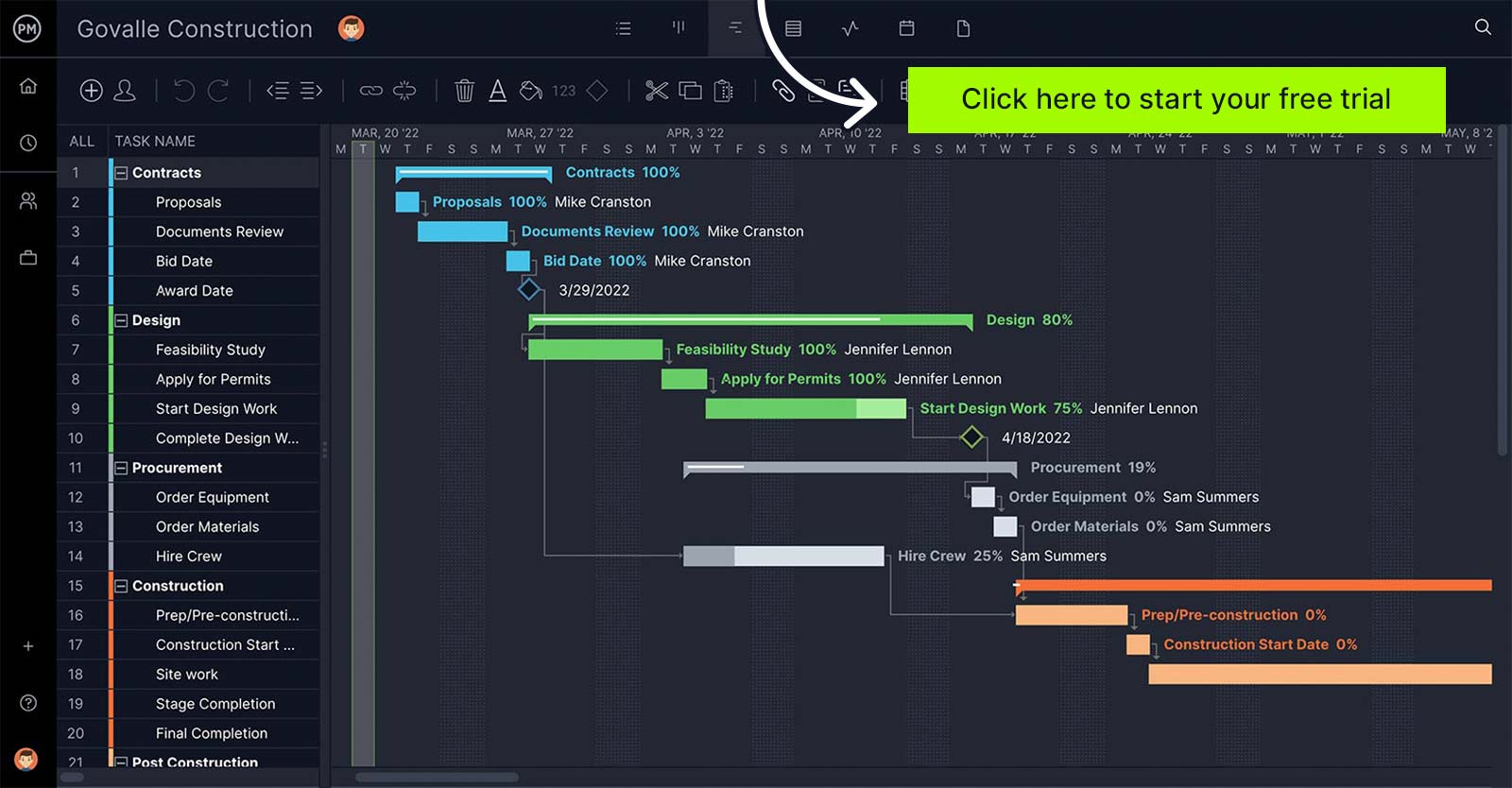
Kaizen Methodology
Kaizen means improvement, but more than just that, it means continual improvement for your business operations. Improvement that is not reaching beyond what it can currently do is static.
Kaizen, more precisely, means change for the better (kai is change and zen is for the better). In terms of business, kaizen means that all activities must be continuously improving. That means everything in the organization, from employees to the CEO. But it’s not just applying to personnel, processes are also included.
The idea was codified by Masaaki Imai, an organizational theorist and management consultant, over 30 years ago with the publication of this book, Kaizen: the Key to Japan’s Competitive Success. Since then, the implications have reached beyond industry and the kaizen principles have been used to help in healthcare, psychotherapy, government, banking and even life coaching.
The kaizen methodology works at constant improvements through the elimination of waste. It’s been around in Japan since after World War II, though influenced by quality management ideas from the United States. It’s part of The Toyota Way, which is a set of principles that support the company’s management approach to production.
Kaizen Principles
The five principles of kaizen are fundamental to any application of kaizen.
- Know Your Customer: Knowledge of who your selling a product or service to is how one creates value. It is key that companies identify their customer’s interests to enhance their experience.
- Let It Flow: This applies to the target of achieving zero waste. It might be an impossible goal, but that’s kaizen for you: if you could achieve that objective improvement would stop. Therefore, everyone in the organization is working towards removing any waste from their corner of the business while also in the process creating value.
- Go to Gemba: The literal translation for gemba is “the real place.” In this context, it’s about leadership and knowing what is happening at every level of the organization. You can think of it as following the action, as value is created where something is actually happening. That’s where you want to be.
- Empower People: This one is directed towards teams and having them organized in such a way that it supports the kaizen principles. Therefore, leadership must set goals for their teams that are not contradictory. They should offer a system and tools to help the teams achieve these goals.
- Be Transparent: Data is the strongest determining factor. It’s the metric that measures success. Therefore, performance and improvements must be tracked with real data
Kaizen in Action
The principles are the guiding lights, the action plan is where kaizen hits the road running. It’s all about organizing, so that the focus is always on improvement and its target are every part of the organization. Everyone is part of the process. A consistent application of the kaizen action plan leads to continuous improvement.
First, take each corner of your organization and look at ways they can be improved. This will involve team collaboration and total involvement from everyone. Individuals need autonomy to take action on improvements themselves, which builds a culture of engagement. This is done with a continuing flow of suggestions and then implementing them to improve the organization.
Each event is outlined by the acronym PDCA, which stands for plan, do, check, act. Begin by setting goals, with documentations and background. Then review what the current state is with that part of the business and plan towards improving it. Identify what improvements will be implemented and try and fix what isn’t working. Report the results, follow-up and repeat.
The idea of always making small improvements is not dissimilar to lean manufacturing, especially with the emphasis of eliminating waste. Kaizen, like a lean or agile approach, works with iterations. It keeps companies flexible.
How Kaizen and ProjectManager Work Together
Ideas are great and methodologies are fundamental to implementing those ideas. But the best plans of mice and men often go astray if they don’t have a project management tool to track their progress. ProjectManager is a dynamic and nimble software that cashes the check that kaizen writes.
ProjectManager has Kanban Boards to Track Progress
What ProjectManager.com provides is a way to monitor that improvement. Kanban is another Japanese work, which translates as signboard or billboard. It also grew from the Toyota Way of manufacturing, offering a visual workflow that increase efficiencies by making sure that the supplies you need now are always on hand, but not more that must be stored.
It’s an elegant system of columns and cards. Each column can have a to do, doing and done heading. Under each of those column headings are cards, which capture the individual task. These cards are then moved from column to column as they’re identified, worked on and completed.
These boards are a great way to track the progress of the improvements. With ProjectManager.com, the kanban boards are even more useful, as they can be assigned to specific team members or a whole group. Then, because the software is online, as teams update their status that information is instantly reflected across the software.
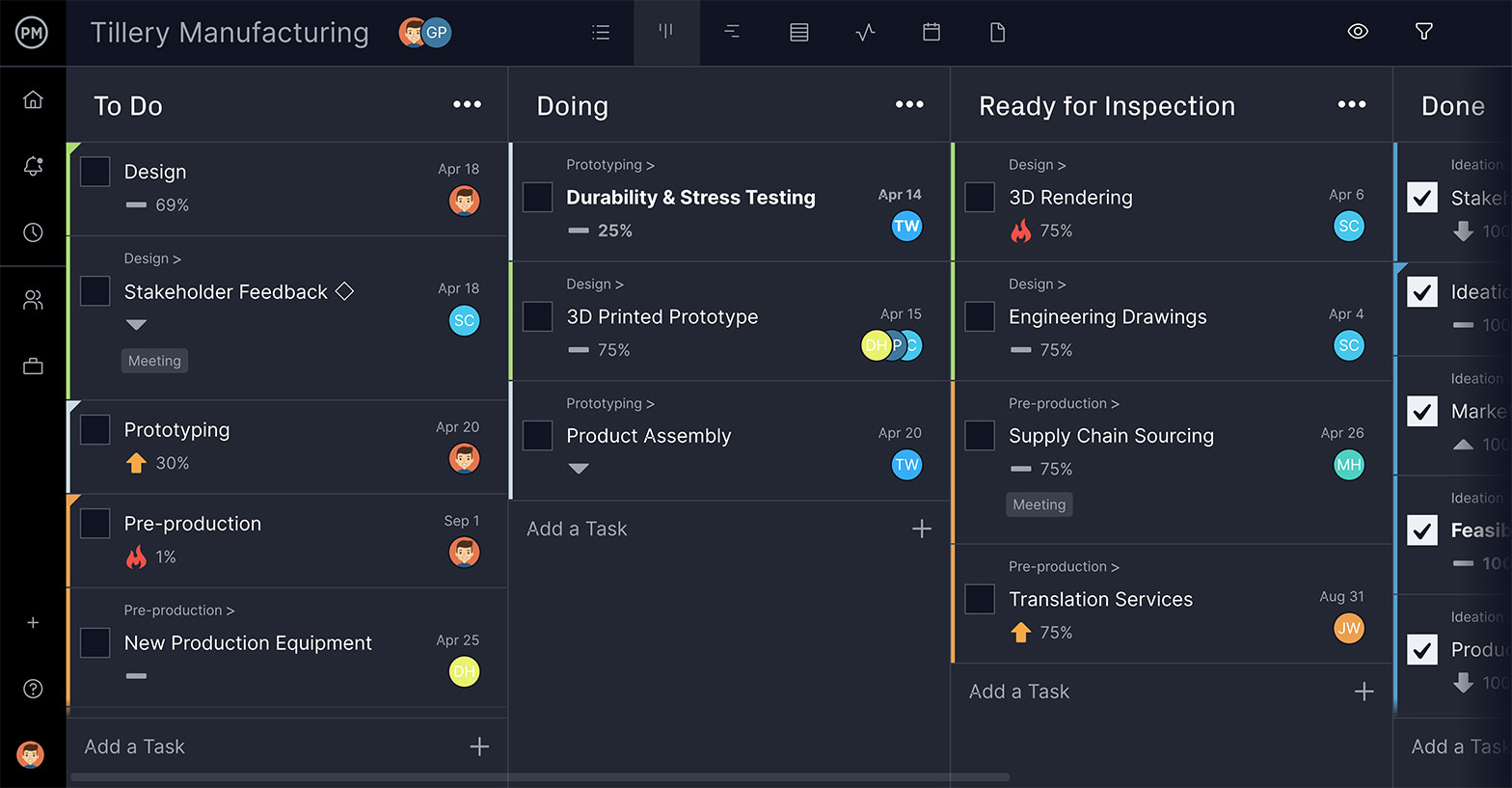
ProjectManager.com’s Real-time Dashboard Tracks Progress
Kaizen encourages collaboration and ProjectManager supports teamwork by giving teams a platform to communicate at the task level. Documents and images can be attached to the card in the board view of our software, so these important files are easy to access. There is a conversation box to dialogue with other team members. When a comment is added, all those assigned the task are notified. It’s especially helpful if your teams are distributed in different sites.
But teams aren’t the only ones who benefit from ProjectManager. Just as kaizen involves the whole organization in making continuous improvements, ProjectManager also gives managers the tools they need to assign easily and monitor the progress of the improvements as they’re implemented.
While project managers can view the progress of the kaizen implementation on the kanban board, they probably are going to want more detailed information. ProjectManager has a real-time dashboard that collects all the data team members input and then crunches those numbers into a series of project metrics that are displayed all in one place.

The real-time dashboard has colorful and easy to read graphs and charts that track progress, workload, timelines and more. These can be shared or printed out for presentation. But in ProjectManager.com, the graphs and charts can be filtered to show just the amount of data you need. This means when a project manager is discussing items with the team, they can go deep into the data, but if the stakeholders need a more general overview, that can be displayed in a click.
Kaizen and ProjectManager.com are a match made in project management heaven. But ProjectManager can do so much more than help you implement change. Our cloud-based project management software can plan, monitor and report on any kind of project. Online Gantt charts makes scheduling collaborative and teams love our easy-to-use task lists and timesheets. See how ProjectManager can improve your project management today by taking this free 30-day trial.