Businesses need to thrive, grow more profitably and stay competitive in a marketplace that is constantly changing. That means increasing their output to the greatest extent possible. The process of achieving that goal is called capacity management.
To understand capacity management, we’ll first fully define the term, list the different types and explain why it’s so important in operations management. Then we’ll discuss some of the strategies involved in implementing capacity management and their benefits.
What Is Capacity Management?
Capacity management is the process of controlling a business’ available capacity to ensure that resources are being used as efficiently as possible. Businesses have a finite amount of resources and capacity management is working to get the most out of their workforce, production, etc. Business capacity measures how much a company can produce or sell over a given period.
Looking at the various resources available to a company and comparing them to the time each needs for a specific project is part of capacity management. Then capacity management analyzes the capacity to get an overview of the composition of the human resources available and whether they are a good fit for the actual needs of the business. This leads to the development of a capacity management plan that addresses the supply and demand of resources.
Capacity management seeks to answer the following questions: are there enough available resources to cover all products and are there enough projects to supply all available resources with enough workload? Some might confuse this for resource management, but there are differences. Capacity management is the first step in project planning. Only after this has been done will management focus on resources, such as assigning teams and allocating tasks.
Being able to monitor resource capacity during the execution of projects is essential to ensuring that a business is maximizing its output. Project management software is a helpful tool in this process. ProjectManager is award-winning project and portfolio management software with features that oversee resources in real time. The team page allows managers to view all the human resources across their projects. They can then see if anyone is over- or underallocated and balance the team’s workload to keep everyone working at capacity to be as productive as possible. Get started with ProjectManager today for free.
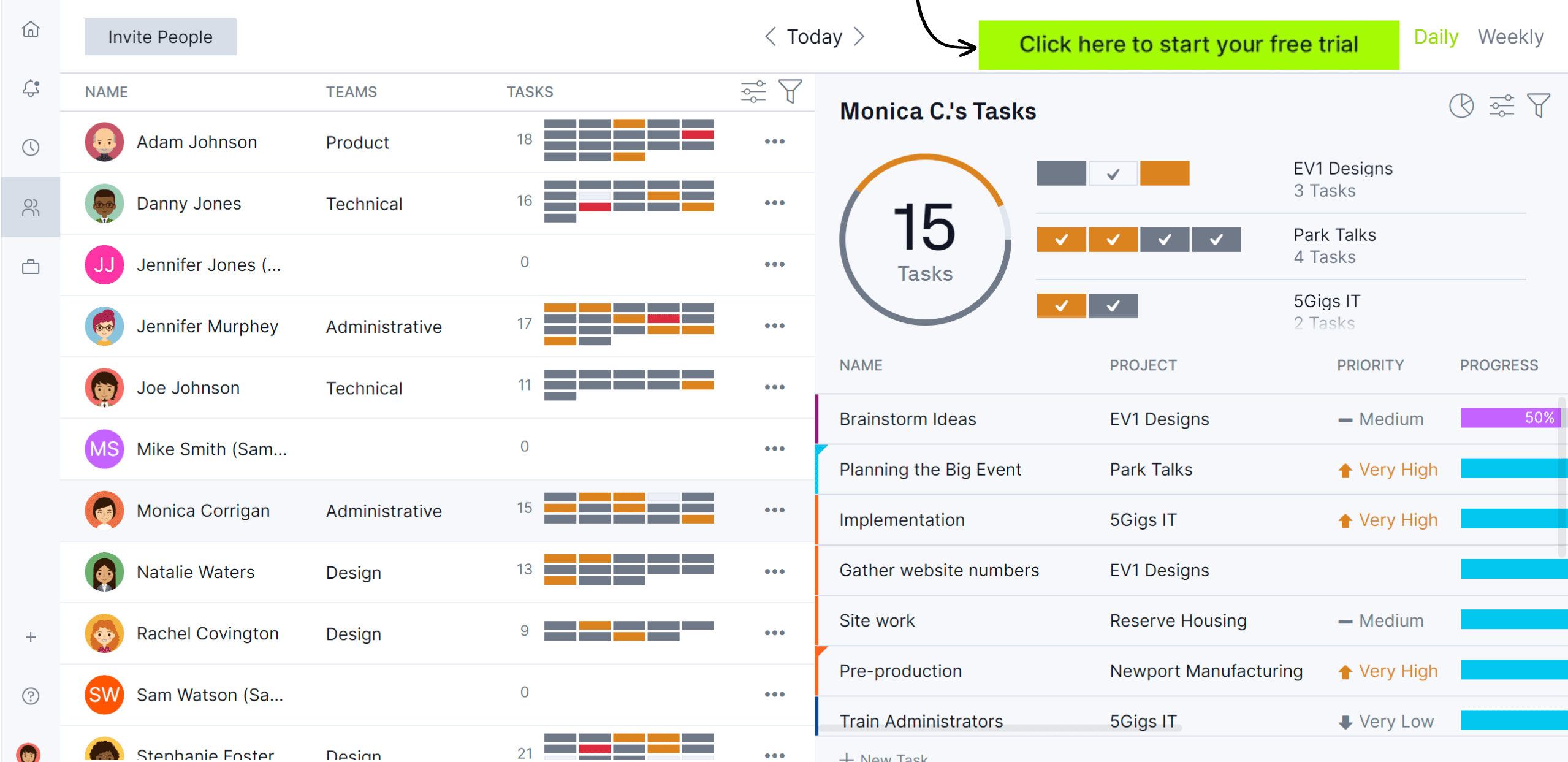
Types of Capacity Management
Different types of capacity management must be managed to get the most out of production. These are potential capacity, which looks at the long term, immediate capacity, which is what’s currently available, and effective capacity, which is the total available capacity that can be put to use. In terms of types of capacity, there are also three types: workforce, production and resources. Let’s review each.
- Workforce Capacity Management: Aligns a company’s human resources with its operational requirements to meet customer demands, achieve business objectives and maintain a competitive advantage. It does this by identifying discrepancies between staff skills and upcoming work needs and making smooth transitions that integrate business strategy with human resource capabilities.
- Production Capacity Management: Seeks to manufacture the greatest amount of output in a production facility. Production capacity is measured in finished products over a given period. This helps manufacturers accurately quote lead times, provide more informed scheduling processes and gauges the efficiency of manufacturing processes and overall performance.
- Resource Capacity Management: Defines the amount of work that can be done by resources at a company, determining tasks and projects that can be completed by those resources over a set period and matches that work with the available resources to meet current and future demand. To do so effectively requires predicting demand, identifying resource gaps and developing and implementing strategies.

Get your free
Capacity Planning Template
Use this free Capacity Planning Template for Excel to manage your projects better.
Proactive vs. Reactive Capacity Management
Proactive capacity management is planning and managing capacity to get the best business outcomes. Reactive capacity management is when managers and their teams respond to emerging capacity issues and try to stop them from negatively impacting performance.
Reactive capacity management can be risky. Following this type of response to capacity issues can lead to not having the resource capacity needed to effectively run projects. It requires visibility into the project so you’re not caught by surprise and unable to fulfill the project’s needs.
Employing proactive capacity management is preferred as it’s a planned method that can meet the anticipated resource challenges. It involves resource forecasting and monitoring to make sure that there are enough resources available and used appropriately to meet current and future project requirements.
By using the long-term process of proactive capacity planning costs are saved, resource utilization is optimized and there is better service quality. This allows businesses to better align resources with their objectives.
Importance of Capacity Management in Operations Management
Capacity management is important in operations management because it helps businesses with their budgeting and scaling so they can identify optimal levels of operations.
In terms of budgeting, capacity management helps businesses determine how their services are offered and the appropriate time frames and staff required to meet current and future operational costs. This informs yearly budgets to better allocate money for expenses.
For scaling benefits, capacity management helps businesses understand if there’s a need to add more staff to help meet anticipated demand based on capacity plans. Not only adding staff but adding specific skills or investing in a larger facility or new equipment is clearer through the lens of capacity planning.
Capacity Planning Template
This free capacity planning template for Excel allows you to estimate the human resource capacity that’s needed to execute a project, process or workflow. It allows you to identify the total available hours for your employees, the total hours that they’re scheduled to work, calculate their utilization rate and estimate costs based on their hourly pay rate.

Capacity Management Strategies
Manufacturers who want to ensure that they’re producing as much as they can to meet demand need to engage in capacity management strategies. Several are commonly used: lag, lead, match and adjustment strategy. All are ways that managers use to grow the business production capacity.
Lag Strategy
In this strategy, managers wait until there’s a surge in demand to act by increasing production and meet the current market demand. This is reactive and puts the business at a disadvantage if demand spikes to unexpected levels, which will be hard to ramp up production to meet. This scenario could result in customer attrition which is why businesses functioning at full capacity use lag strategy.
Lead Strategy
With a lead strategy, a business will increase its production capacity before a surge in demand. Of course, this assumes there will be an increase in demand just around the corner and the additional output will cover that increased demand. This strategy is better suited for larger companies that can warehouse excess inventory and the costs associated with it or even sacrifice stock that doesn’t sell.
Match Strategy
Match mixes lag and lead strategies. Businesses increase capacity after analyzing current market demands. But these increases are small until it becomes clear that demand is going through the roof. Then the business increases production to meet that demand. Again, these increases are always small and incremental, which allows the business to work on expanding sales.
Adjustment Strategy
This is similar to the match strategy as it uses both lag and lead strategies, but the adjustment strategy is more data-based. It uses planning tools to analyze multiple variables, such as demand forecasts, real-time sales data and seasonal trends. Thereby, capacity is adjusted more accurately in advance of demand.
Benefits of Capacity Management
Capacity management helps businesses be as productive as possible and meet the fluctuating market demand. But that’s only the start when it comes to the benefits of capacity management. Here are some other reasons to employ this process when manufacturing products.
- Improves cost estimates, especially during growth or recessions, by identifying sudden shifts in prices
- Optimizes production efficiency by scheduling production cycles ahead of time
- Reduces the general cost of doing business
- Helps with inventory management and issues within the supply chain
- Allocates resources better
- Provides operational analysis when thinking of growing the business
How ProjectManager Helps Monitor Resource Capacity
Capacity management relies on the close monitoring of production. It’s only through tracking and analyzing data that significant improvements can be made to manufacturing processes that will lead to greater capacity utilization. Project management software can help to provide the key performance indicators (KPIs) that will direct how to work more efficiently. ProjectManager is award-winning project and portfolio management software that has multiple project views that are all capturing live data and updating together in real time.
Allocate and Schedule Resources with Multiple Views
When onboarding team members, managers can set their availability, including PTO, vacation and global holidays. That makes it easier to allocate resources. Those resources can be scheduled on robust Gantt charts that organize tasks on a timeline but can also link all four types of task dependencies to avoid costly delays. Once the schedule is made, set a baseline and the software automatically compares planned versus actual progress in real time to keep work on track.

Track Labor Costs with Timesheets
Progress is one area of improvement to add capacity to production, but it’s not the only one. Reducing costs should also be on the forefront of a manager’s mind. There are several ways to track costs. One is with secure timesheets that streamline payroll, but also provide visibility into how far each team member has gone to completing their tasks and the labor costs associated with that. For a high-level overview, toggle to the real-time dashboard, which tracks many KPIs, including costs, with easy-to-use graphs and charts.
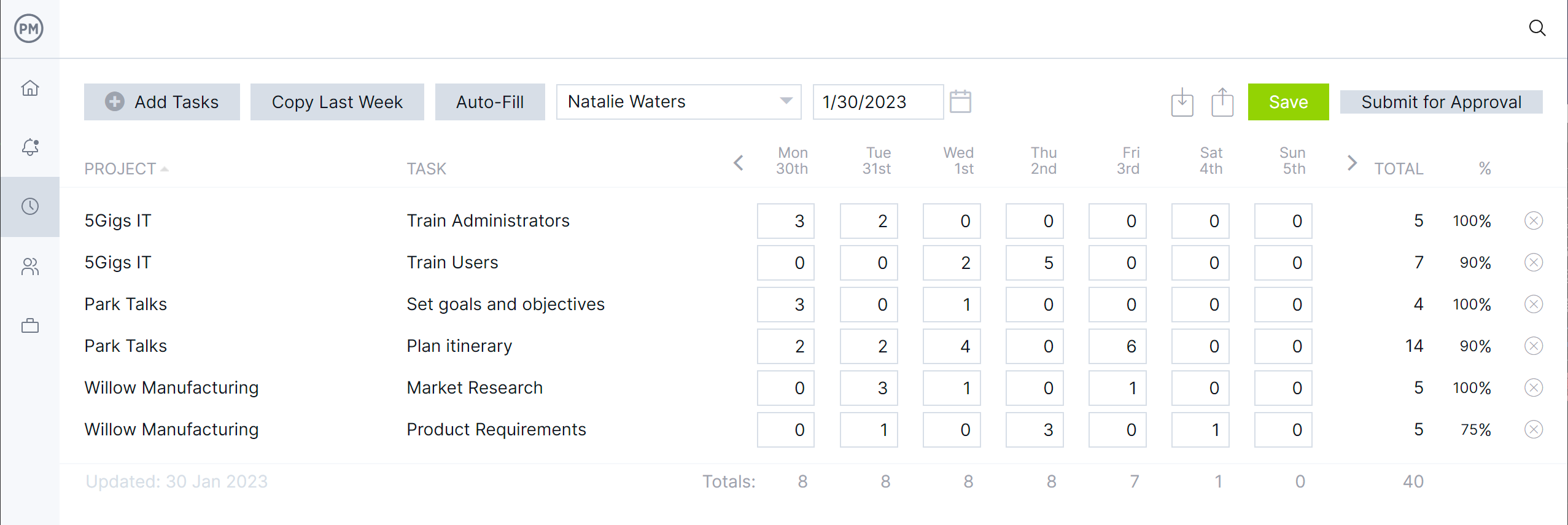
For a more detailed look at metrics, and to keep stakeholders informed on capacity, use the customizable reporting features. Reports on status, portfolio, workload, timesheets, variance and more can be generated with a keystroke. They can be filtered to show only pertinent data and shared across multiple formats with stakeholders.
ProjectManager is online project and portfolio management software that connects teams whether they’re in the office or on the factory floor. They can share files, comment at the task level and stay updated with email and in-app notifications. Join teams at Avis, Nestle and Siemens who use our software to deliver success. Get started with ProjectManager today for free.