Managing construction projects is complex and stressful. You may stick to your schedule and budget, but if your project doesn’t meet quality acceptance criteria, then you’re not just going to upset your stakeholders; you might face lawsuits.
Quality means different things to different people, which is why you should adhere to construction quality control. It’s a quality management system that allows you to define what quality is, track it and make necessary changes to ensure those benchmarks are met.
What Is Construction Quality Control?
Construction quality control is a management system aimed at ensuring the final deliverable meets the standards and guidelines set by the client. That includes completing the project within the scope of work and avoiding disputes throughout the life cycle of the project. Quality is defined by the client, regulatory agencies and environmental and policy guidelines. All these quality assurance requirements and procedures are documented in a construction quality management plan.
Construction quality is controlled by good monitoring and tracking of your project. ProjectManager is online project management software that delivers real-time data, so you can catch issues before they become problems. Try ProjectManager free today!
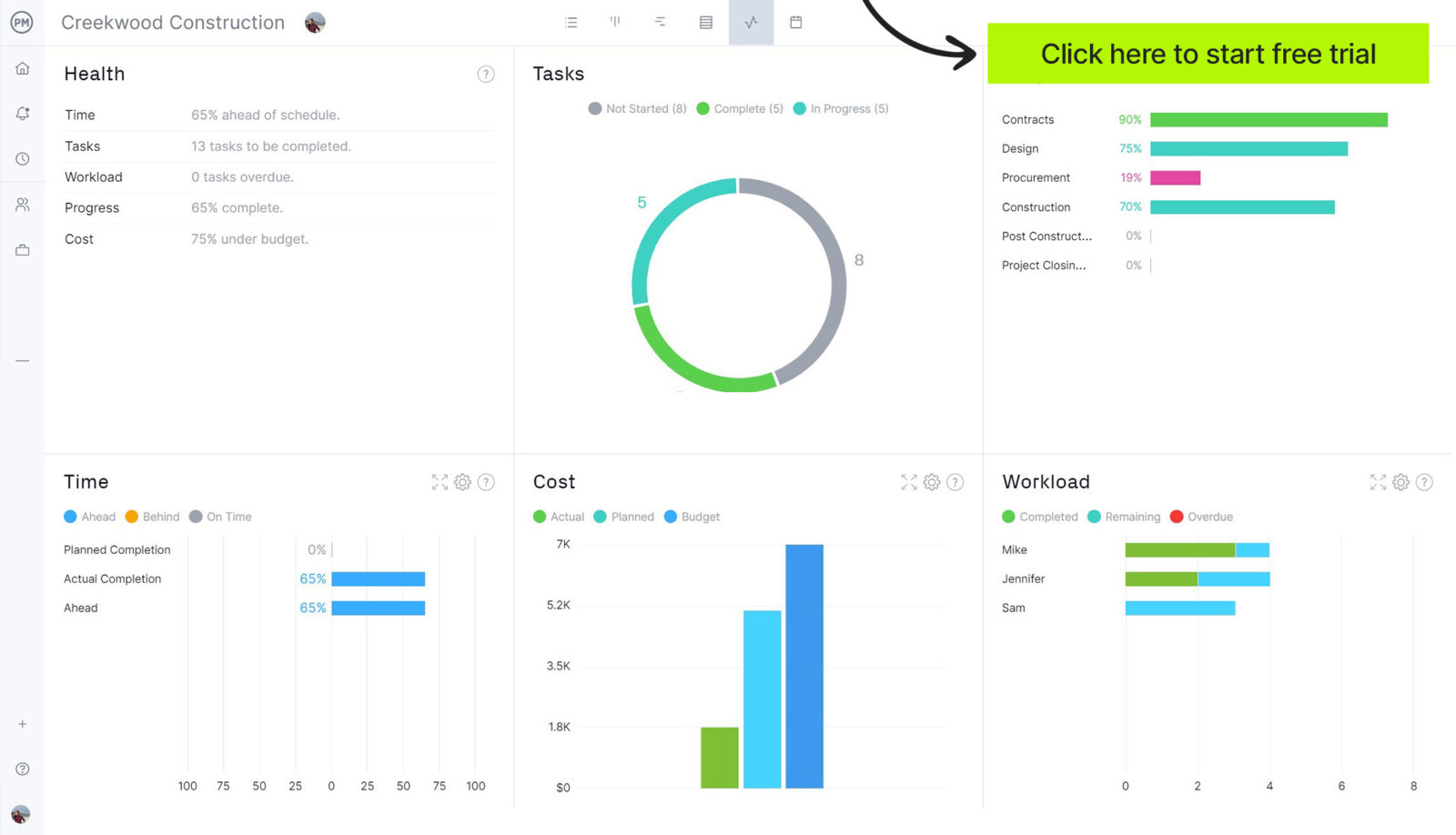
Before further defining the construction quality control process, it’s important to understand the difference between construction quality control and construction quality assurance.
Construction Quality Control vs. Construction Quality Assurance
There are two aspects of project quality management in construction: construction quality assurance (QA) and construction quality control (QC). Quality assurance sets the quality management expectations and standards, while construction quality control focuses on establishing procedures to measure whether those quality standards are being met or not. The construction quality control manager drives this construction quality control plan throughout all phases of the project.
What Is a Construction Quality Control Plan?
A construction quality control plan is a document that highlights the specific processes and procedures a construction team uses to ensure project quality. This is an essential part of construction project management as it helps meet (and exceed) client expectations, reduce risks and costs, improve efficiency and enhance safety. As a result of this document, construction teams can significantly improve their quality of work and build a respected reputation in the industry.
What Should Be Included in a Construction Quality Control Plan?
When putting together a construction quality control plan, you need to address quite a few things. Here is a list to keep you from missing any of the important steps:
1. Project Specifications
In this section, outline the technical requirements of the project as this will be the foundation for quality control. This includes construction plans, design drawings and detailed specifications for materials, workmanship and finishes. State all applicable codes, standards and contractual obligations. If there are project-specific requirements like sustainability certifications, be sure to include them here.
2. Quality Objectives and Standards
This is where you define the quality assurance standards for the project, which is done by collecting client specifications and expectations for the quality of the finished build. The objectives may include ensuring that the materials meet industry standards, regulatory requirements and client specifications. The materials should also achieve defect-free construction and minimize rework. Safety and environmental standards should also be considered in this section. Having clear quality objectives helps guide the team toward consistent outcomes while minimizing defects.
But you’ll also want to go beyond their needs and address specifications from building codes and industry standards. Lay it all out so there’s no confusion on why the work was done the way it was done.
3. Quality Control Roles and Responsibilities
In this section of the construction quality control plan, define the roles and responsibilities of the personnel involved in quality control. This includes roles such as the quality control manager who implements the plan as well as inspectors who oversee daily compliance. Subcontractors, suppliers and construction project managers should also understand quality control obligations. In many cases, an organizational chart is included to help clarify who is responsible for what. Below is more detail on each of these roles.
- Quality Control Manager: Choose someone to lead the effort—a quality control manager. The client needs to know who this person is and why they’re qualified for the position. The quality manager leads all quality management work and is responsible for the day-to-day field operations. The construction quality control plan needs to define the quality manager’s responsibilities and how they work with the rest of the crew.
- Quality Control Inspectors: These inspectors play an important role in ensuring the quality and safety of the project. They enforce building codes and standards, monitor construction activities, perform inspections and document findings for reports. If needed, they communicate with stakeholders as well.
- Subcontractors and Suppliers: First, inform your client of the suppliers and materials in use. Since these are organizations outside your governance, you need to add selection criteria for suppliers and subcontractors to your construction quality control plan. This includes price, naturally, but also if they’re delivering on the quality you expect.
Quality Control Procedures
Quality control in construction can’t happen without quality control procedures in place. In this section, outline the actions and processes needed to ensure quality at every stage of the project. This includes an inspection test plan (ITP) that notes when key inspection and testing activities will take place during various stages. During this stage, procedures for conducting quality control inspections, tests and audits are outlined. All of these processes work together to ensure the project has consistent quality management.
- Inspection Test Plan: Create an inspection test plan (ITP) to decide what is inspected, the construction quality control methods that will be used and let the team know when it’s inspected. Also, there must be a person responsible for carrying out the inspection, whether that’s someone in your crew or a third party.
- Quality Control Inspections and Tests: Inspect each phase of the construction as part of the overall construction project management of your build. Conduct tests to verify the quality of material used or the functioning of quality management systems. List the inspections and tests you will perform over the life cycle of the construction project, including the forms and test results you’ll use.
- Quality Control Audits: This is a systematic and independent examination of an organization’s quality management system (QMS) or the processes within it. This is a critical tool for organizations that want to ensure product quality, services and operations.
- Corrective Actions: No construction project ever goes completely as planned. When things go wrong, you need to have corrective actions in your plan in order to maintain the overall quality of the project. There should also be a record documenting these changes and how they were implemented, such as a decision log.
- Punch List and Final Walkthrough: This is where you outline how the final construction quality control inspection will be conducted, including what the punch list will look like and how the final walkthrough with the client will be conducted.
- Surveillance: Have monitoring be part of your construction quality control plan. You need to let your client know how you’ll monitor quality. Decide on the frequency of surveillance as well as how and what you’ll be monitoring. Detail this in the construction quality control plan.
Materials and Equipment Quality Control
In this section on quality control in construction, the focus is on ensuring that the used materials meet the requirements for safety, strength and durability. This includes material selection and testing, material handling and material inspection. We’ve broken down various aspects below.
- Material Submittal and Approval Process: Contractors will submit information about the materials and products they intend to use in a project to the design team for review and approval. Usually, the materials to be used are described in a bill of quantities document.
- Material Testing: This involves looking at the physical and mechanical properties of materials to ensure they meet the needed standards and requirements.
- On-site Material Storing Protocols: This is essential for safety, efficiency and overall project success. It ensures that all materials are stored securely and properly to reduce the risk of injury and follow compliance with regulations.
- Calibration of Equipment and Maintenance: Periodic equipment calibration and a clear maintenance schedule help ensure that construction tasks can be completed accurately.
- Vendor Quality Audits: This is a systematic evaluation of a vendor’s ability to consistently deliver the products or services that meet the needed quality standards.
Communication and Reporting
Quality control should be part of the discussion between the project owner and whoever is executing the construction project from start to finish, whether that is a general contractor or multiple subcontractors. Quality control should be part of the reports, test results and any inspection data. Your construction quality control plan must have a communications guideline to explain how, and with what frequency, this communication will occur.
Some examples of construction quality control reports include:
- Non-conformance reports (NCRs)
- Corrective action reports (CARs)
- Root cause analysis reports
- Quality audit records
- Testing logs
- Final inspection report
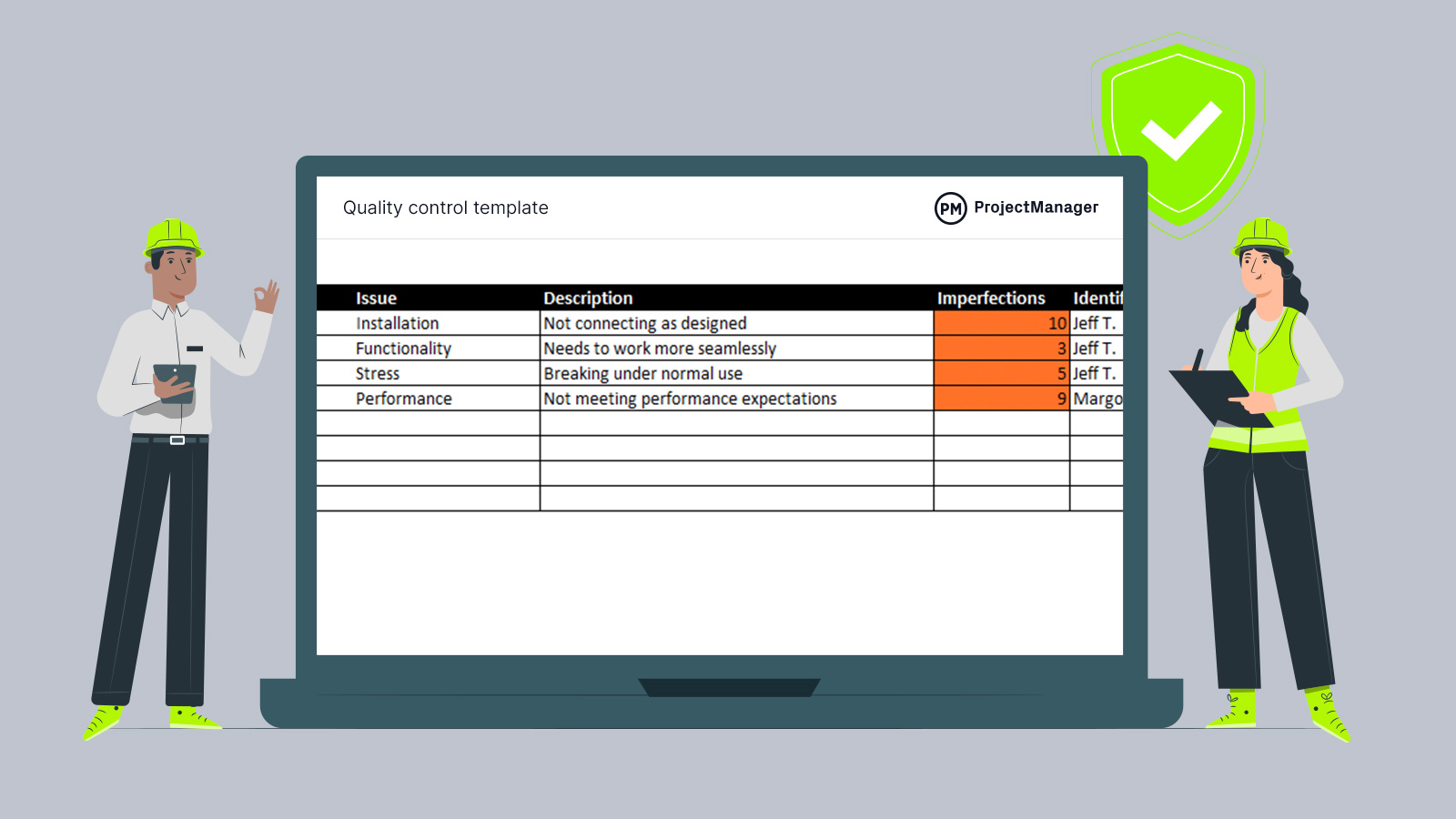
Get your free
Quality Control Template
Use this free Quality Control Template for Excel to manage your projects better.
Construction Quality Control Checklist
After making a construction quality control plan, it’s still important to prepare a quality control checklist to make the process of inspection thorough and less likely to overlook items. A good construction quality control checklist should summarize the contents of the construction quality control plan in a much simpler and easy-to-read format.
Here’s a comprehensive construction quality control checklist to help you manage quality as your construction project is executed.
- Conduct preconstruction quality meetings
- Inspect the site conditions and create a site inspection report
- Review project specifications, drawings and plans
- Confirm that all permits and approvals are in place
- Create an inspection test plan
- Ensure equipment is well maintained and works properly
- Check material deliveries to ensure they meet quality standards
- Establish best practices for material and equipment storage
- Implement various construction quality control inspection methods as applicable
- Perform daily or weekly inspections at the job site
- Document all quality defects using non-conformance reports
- Keep project stakeholders informed on quality inspections
- Use a punch list to ensure all quality defects are fixed
- Prepare a final quality report and submit documentation to the project owner
Why Construction Quality Control Matters
Your project isn’t a success if your client isn’t satisfied. Construction quality control is important because it improves client satisfaction. A happy client will work with you again, and even give recommendations to others. More practically, doing quality work means less rework. Not needing to redo work that should have been done right the first time reduces costs and keeps you on schedule. This is also a way to keep the morale of your crew high, which in turn means they’ll work more productively.
Most important, though, is that construction quality control leads to a successful project. Everything done in construction project management rests on the quality of your work. Focusing on quality means fewer problems and changes, while also saving time and money.
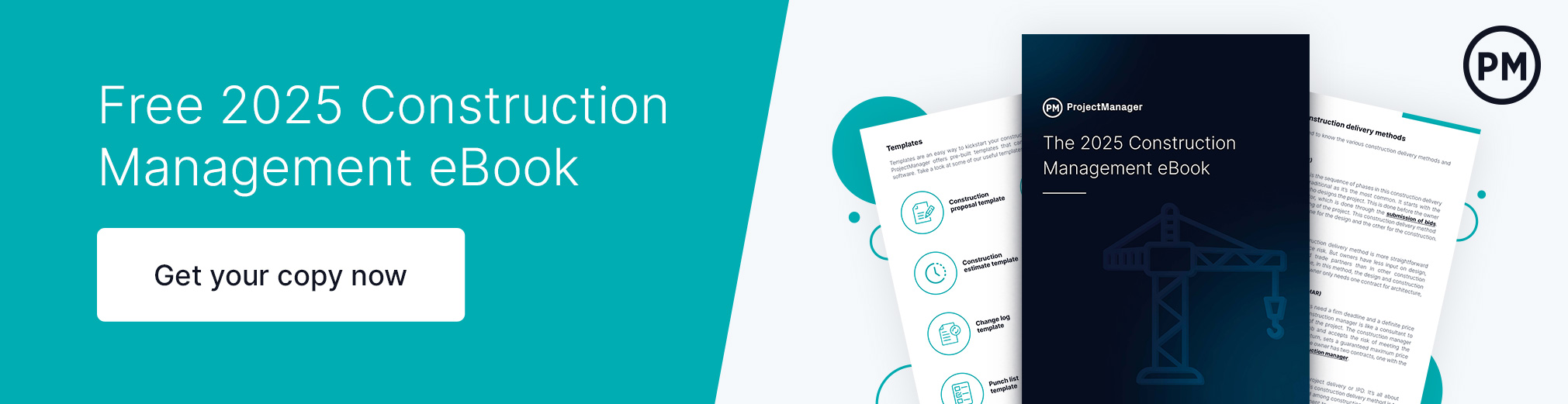
Construction Quality Control Inspection Methods
Here are the some of the most commonly used construction quality control methods to ensure materials, workmanship and other aspects of a construction project meet quality objectives:
1. Non-Destructive Testing
This is a collection of techniques that evaluate the properties of materials, systems, components and other project resources without causing permanent damage. It helps in areas such as safety, quality control, cost savings and maintenance.
- Ultrasonic Testing (UT)
- Radiographic Testing (RT)
- Magnetic Particle Testing (MPT)
- Dye Penetrant Testing (DPT)
- Ground Penetrating Radar (GPR)
2. Destructive Testing
In quality control in construction projects, destructive testing includes subjecting materials or components to conditions or stressors that could cause failure or permanent damage. These tests are designed to offer important data on the material’s strength and behavior under extreme conditions.
- Compressive Strength Tests
- Tensile Strength Tests
- Pull-Off Adhesion Tests
3. Structural Load Testing
In this aspect of construction quality control, the structural integrity and capacity of buildings (or other structures) are verified. This may include design verification, identification of defects, static load tests, proof load tests, etc. It can lead to improved safety, reduced risk and improved quality.
4. Sample and Laboratory Testing
This helps ensure the quality, safety and performance of construction projects. The process involves collecting samples of materials from the construction site and putting them through tests in a controlled environment to determine if they’re suitable for their intended use. The goal is to verify material quality, prevent failures and ensure compliance.
5. Visual Inspection Methods
Visual inspection is a widely used method to assess quality in construction. This approach typically involves the human eye that’s aided by simple tools to look at the materials, components and work in progress for defects or irregularities. This happens to check for material inspection, workmanship inspection and safety inspections.
6. Mock-Up Testing
This is used to evaluate the design and construction details in a real-world environment. The key purpose is to offer visual and aesthetic review, functionality and performance testing, problem identification and resolution and collaboration. It helps reduce the risk of expensive rework and change orders, improves quality, increases safety and improves client satisfaction.
Quality Control Template
This quality control template is ideal for managing the quality of deliverables in a construction project. You can use it to log any quality management issues that are found at the job site, including who found the issue, the date when it was found and its priority level among other important quality management information.
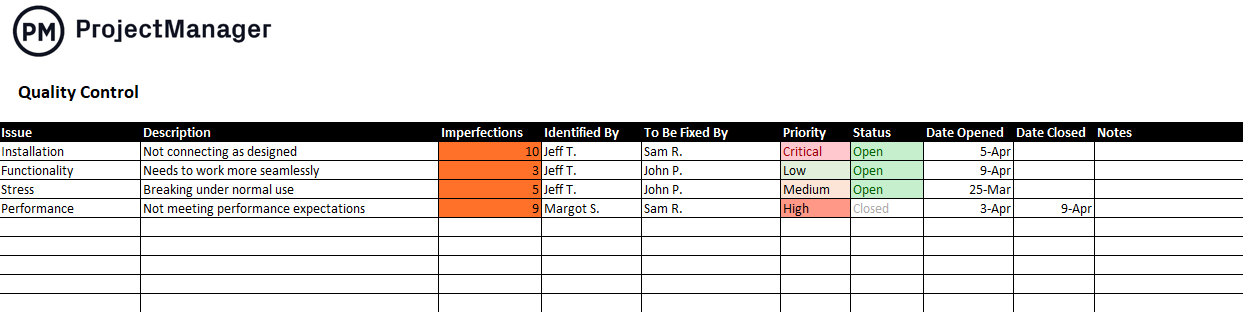
We offer a variety of free construction project management templates for Excel you can use to manage all aspects of your project.
How ProjectManager Helps With Construction Quality Control
Managing the quality of construction projects involves close monitoring of the work. To streamline this process, you’ll want to use construction project management software. ProjectManager is online software that gives you the real-time data you need to respond and meet your client’s quality expectations.
Organize Construction Plans on Gantt Charts
Organize all the tasks associated with your construction quality control plan with an online Gantt chart. ProjectManager lets you link dependencies, set milestones and filter for the critical path. Then you can set a baseline to compare actual progress against the planned effort. The Gantt can be easily shared with your client to keep them updated.
Track Your Plan’s Progress on Dashboards
ProjectManager’s live dashboard gives you real-time data on several project metrics, so you can catch any irregularities that might impact the quality of the work. There’s even a portfolio dashboard if you’re managing several projects at once.
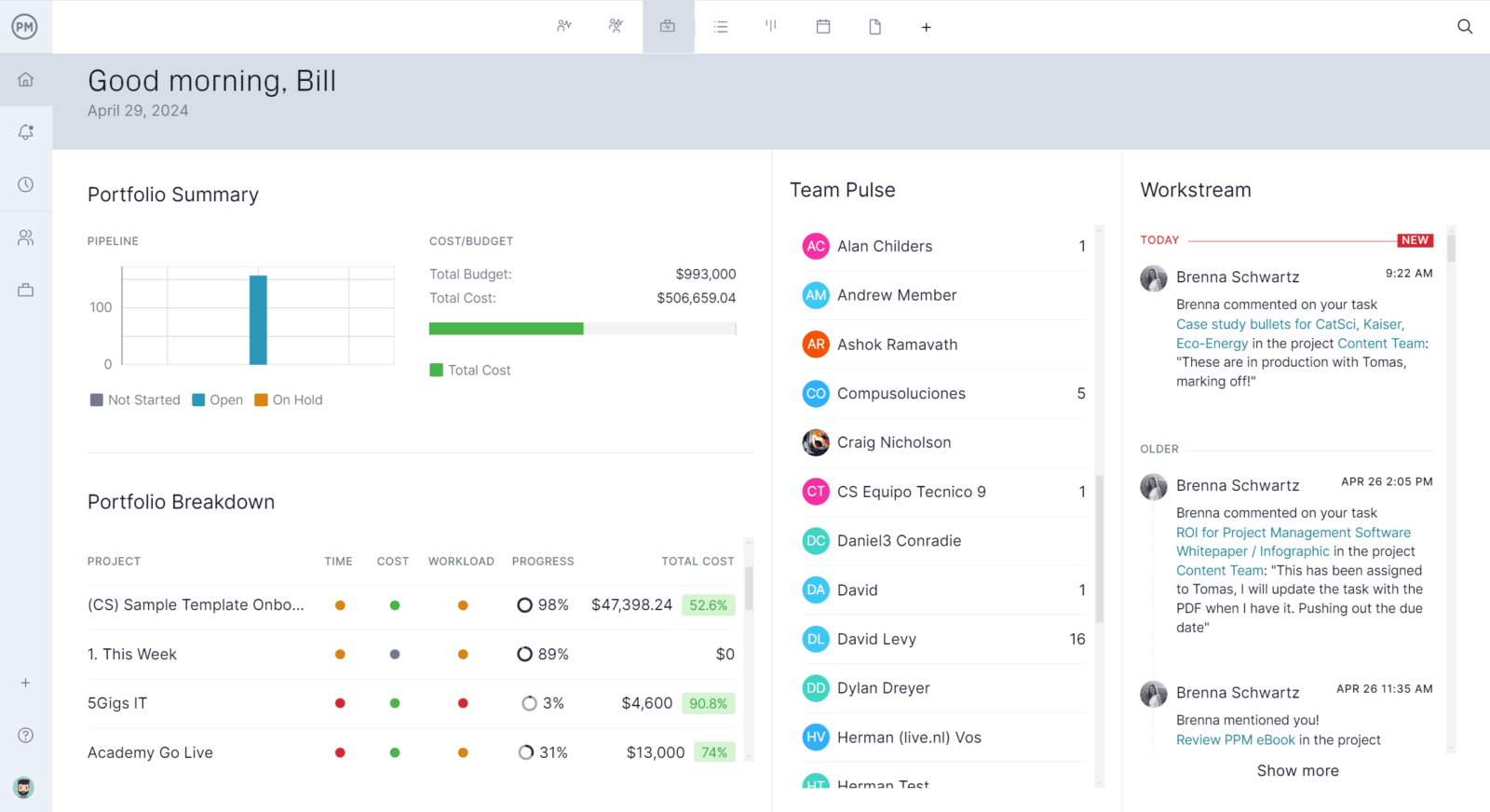
Create Reports for Stakeholders in Seconds
If you want to take a deeper dive into project data, use ProjectManager’s one-click reports. These are especially helpful for clients that don’t want to get granular but want to know if you’re on time, within budget and are meeting quality expectations. Share reports by email or print them out, depending on what the client prefers.
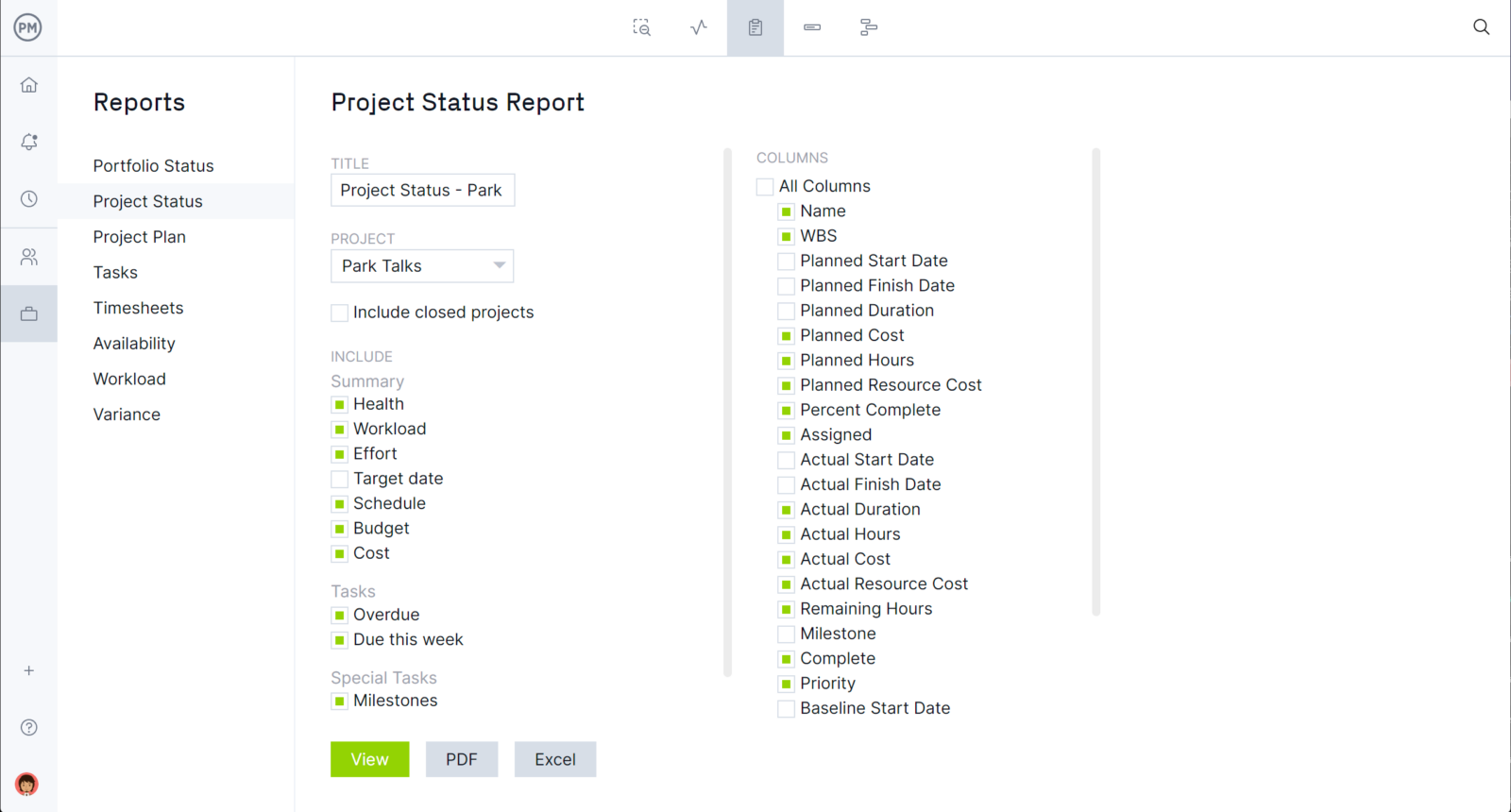
ProjectManager is award-winning software that organizes tasks, teams and projects. Use ProjectManager to foster communications and control the quality of your construction project. With resource management, timesheet and task management features, ProjectManager can help you create a construction quality control plan, quickly find problems and resolve them before they impact time or costs. Try ProjectManager free today.