The relationship between supply and demand is Economics 101. Whether a business is manufacturing or managing a warehouse, understanding demand management goes a long way to ensure that stock levels are always balanced with customer needs.
This requires first an understanding of demand management and how it benefits business. Next, we’ll outline the demand management process to learn how to implement this planning methodology and how software can facilitate that process.
What Is Demand Management?
Demand management is the process of managing customer needs for a product that a company sells. It’s a planning methodology that tries to forecast what a customer will want, when they’ll want it and the logistics of getting that product to them. By planning, companies can identify and avoid potential problems, such as bottlenecks in production or the supply chain and market volatility.
In manufacturing, demand management comes after supply chain management, such as managing procurement and suppliers, but before portfolio management. Demand management is cross-functional as it crosses many disciplines, from consumer demand, supply teams and inventory to marketing and customer service.
One way to look at demand management is as a bridge between the marketplace and a company’s internal operations. That is, demand management works to create interactions between operations and marketing with the goal of being able to develop actions that align the fluctuations of the market with a company’s strategy, production capacity and customer needs.
Managing production is key to demand management and project management software is essential to that process. ProjectManager is award-winning project and portfolio management software with resource allocation features to keep teams working at capacity. Use the team page or the color-coded workload chart to monitor your team’s allocation. If some are over- or underallocated, the team’s workload can be balanced quickly to keep them as productive as needed to meet demand. Get started with ProjectManager today for free.
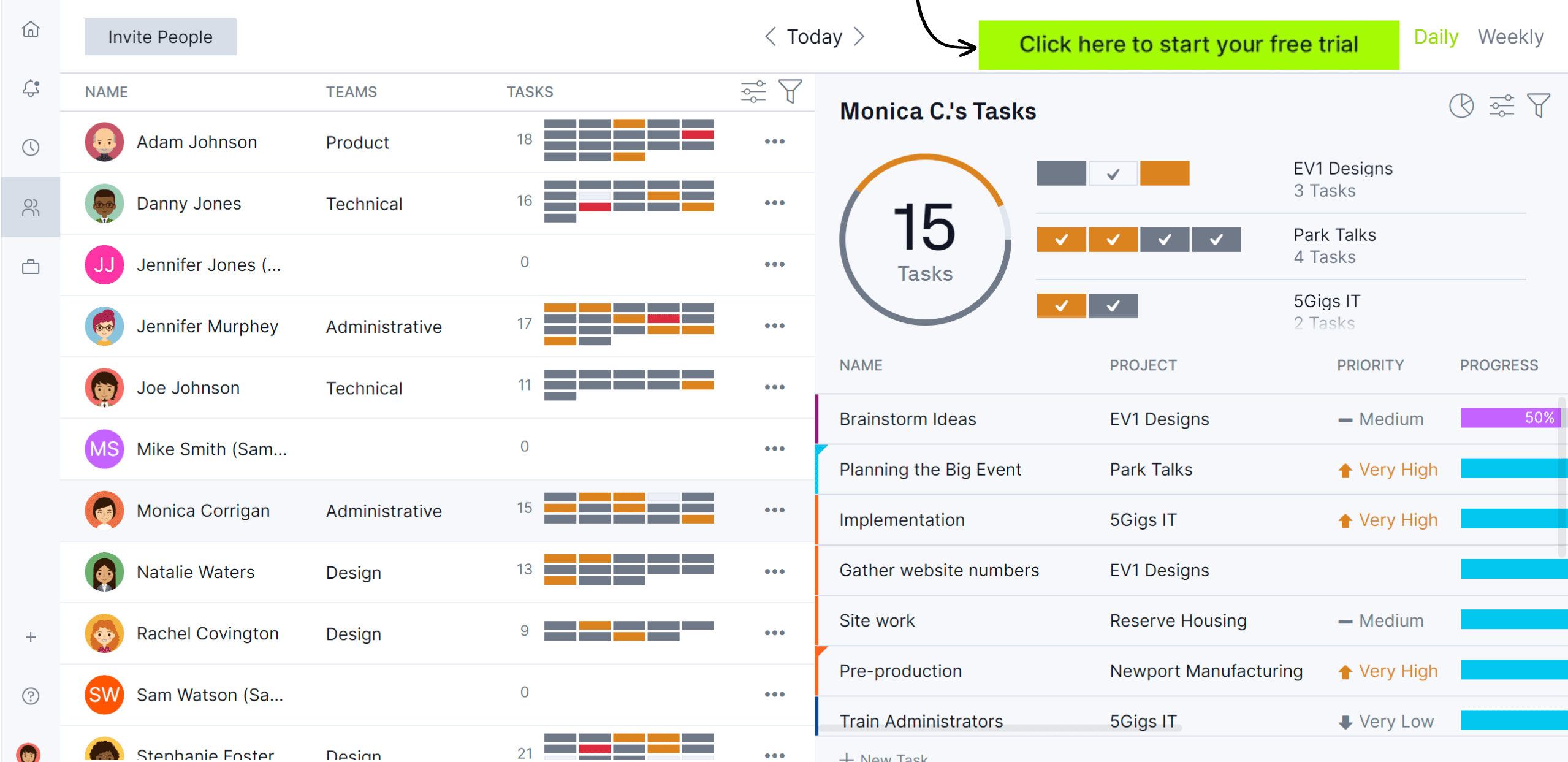
What Is the Importance of Demand Management for Businesses?
Understanding customer demand will benefit any business that manufactures or sells products. Demand management is a crucial part of any business strategy so they have stock on hand to meet customer needs. Here are some other reasons that illustrate the importance of demand management for businesses.
Helps Organizations Establish their Production Budget
Demand management allows companies to analyze and predict changes and trends in market demand. This leads to a reduction in costs due to overproduction or stockouts. It also informs the production budget to make sure that there are enough funds to meet demand but not add unnecessary costs through excess inventory, labor, etc.
Allows Businesses to Meet Customer Demand
Knowing what customers want allows for better planning of delivering it to them. If there’s a spike in customer demand or if customer demand is waning, production planning must follow suit or suffer a loss in business or the cost of carrying unwanted inventory. Demand management allows for a better gauge of customer demand.
Prevents Excess Inventory and Overproduction
As stated above, excess inventory is costly. All that product must be stored, which leads to money spent on items that aren’t being sold. Ideally, a company wants a warehouse full of inventory that will move due to a balance between what’s in stock and the customer demand. Demand management is a way to achieve that balance.
Helps With Supply Chain Planning
Supply chain planning is all about optimizing the manufacturing and delivery of goods. It starts with raw materials, moves to finished products and ends with customers. A clear picture of customer demand will inform these steps, from knowing how much raw material is needed to the quantity of items produced, etc. Demand management, then, is an integral part of this process and helps a business spend only what it needs.
Informs Workforce Planning
Demand management helps managers understand the current and future workforce requirements, which allows them to plan better. The managers better understand customer demand, which leads to knowing how to allocate resources to meet that demand by having the right people with the right skills.
Demand Management Process
Demand management helps businesses to oversee and manage customer demand. To do this, though, requires a process. The demand management process includes knowing what customers want and the steps necessary to fulfill those needs. To plan for current and future demand requires following these six steps in the demand management process.
Demand Forecasting
Demand forecasting is the process of predicting customer needs for a business’ products. That demand determines what adjustments need to be made or if new offerings should be added. Estimating what customers want and how much of each item they’ll want isn’t an exact science. To get an accurate estimate, businesses use many methods, some qualitative and other quantitative. Data, software and analytics are all used in this process, but predictions should always be hedged by noting their strengths and weaknesses.
Demand Planning
Once the forecast is clear, the planning begins. Demand planning is part of the demand management process that enables a business to plan to meet the demand forecast through the production of its products. This is also part of the larger supply chain process and requires an understanding of horizon (timeline for the demand plan), frequency (how often the plan is updated) and granularity (level of detail in the plan). This allows for the creation of a demand plan that meets customer needs.
Demand Modeling
One way to make a more accurate demand forecast and, therefore, have a better demand plan is through demand modeling. Demand modeling uses predictive analysis to understand customer behavior. It looks at things such as the propensity of a customer to purchase a product and how the propensity changes based on things like the price of that product. Historical data is also used to better understand the customers’ behavior.
Demand Capacity
Demand capacity is a ratio that compares the production that a company makes with the demand coming from its customers. When manufacturing, businesses measure demand capacity to make sure they have the production capacity levels that allow them to meet the demand for their products. Calculating this uses several sources, such as sales records, customer feedback, inventory levels, production reports or service logs.
Demand Sensing
Another way to predict customer demand is with demand sensing, which uses real-time data and analytics to understand and predict what a customer will want, when they’ll want it and how much they’ll want. This is done by reviewing sales history, inventory levels and customer behavior, point-of-sale systems, online sales platforms and customer surveys. While not perfect, demand sensing can reduce forecast error by up to 50 percent and increase accuracy by up to 20 percent.
Demand Shaping
Demand shaping is a supply chain strategy that uses tactics such as price and promotion incentives, product substitutions and cost modifications to lure customers to buy specific products. Through these means, a business can influence demand for a certain item to match its planned supply.
What Does a Demand Manager Do?
The person responsible for the demand management process is a demand manager or demand planning manager a professional tasked with overseeing the daily operations of the demand planning team, who analyzes customer and vendor demand to create and refine their forecasts.
Demand managers are responsible for reviewing purchase history, sales history and the marketing strategies businesses use to promote products and stimulate growth. They also evaluate their effectiveness and respond accordingly to improve.
To do this, the demand manager will come up with effective forecast models based on industry trends and demand patterns. They’ll implement solutions to improve the accuracy of demand forecasting, as well. They are highly analytical and have a deep knowledge of advanced mathematical and forecasting policies.
How to Manage Production With ProjectManager
Demand management has a great influence on production. It tells manufacturers how much of a product customers want so they can produce just the right amount or as close to that number as possible. This saves money on labor, storage and more. However, demand management can’t help create a more effective production plan, but project management software can. ProjectManager is award-winning project and portfolio management software with multiple project views to plan production activities, schedule resources and track labor costs to ensure that manufacturing goes according to budget.
Plan Production Activities
Managers can plan their production activities on robust Gantt charts that link all four types of task dependencies to avoid delays. Once the schedule is made, resources allocated and costs determined, set a baseline to capture that plan so it can be compared to actual progress and costs during production. Real-time dashboards capture key performance indicators (KPIs) on easy-to-use graphs and charts for a high-level overview of production. There are also customizable kanban boards with columns that reflect the production cycle and cards that track costs, progress and schedule resources. Use kanban to manage order fulfillment, too.

Track Labor Costs With Timesheets
Keeping a close eye on labor costs helps manage production costs. Employees can use timesheets that automatically add their hours and are securely sealed once sent to a manager to review and pass onto payroll. While this streamlines the payroll process, it’s only part of what timesheets can do. Timesheets capture labor costs and let managers see how far each team member is in terms of completing their assigned tasks. This allows managers to calculate whether the production is progressing as planned or if resources need to be allocated to get back on track.
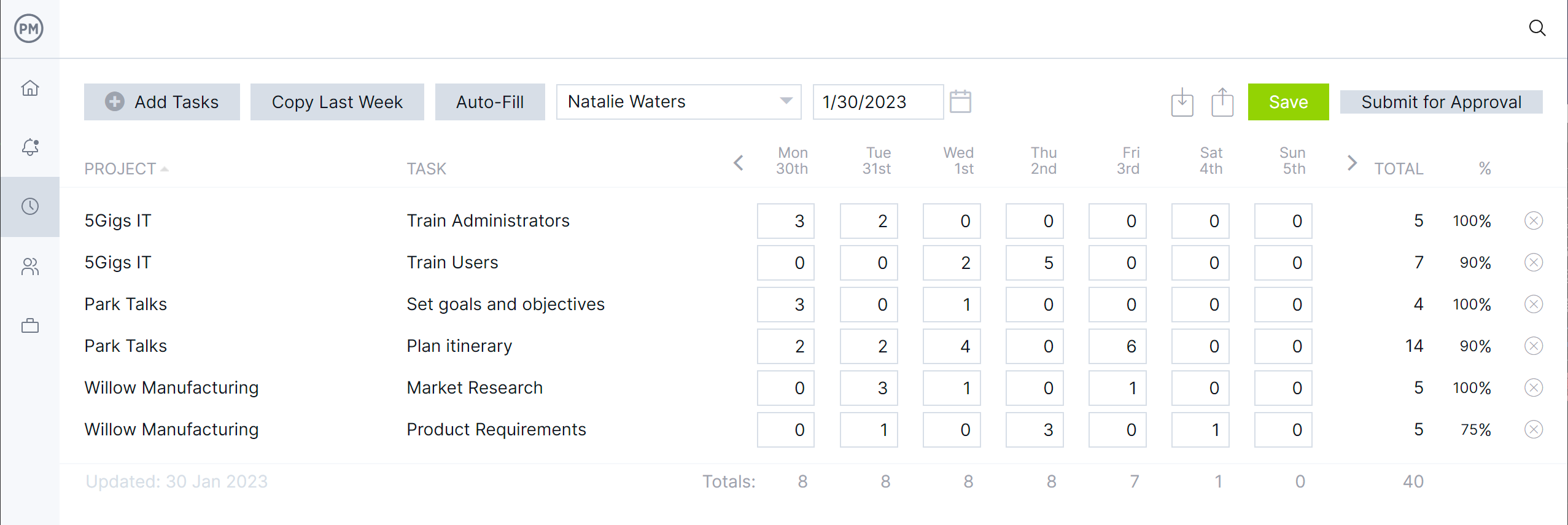
Stakeholders can stay up to date with production by using one of the multiple project views to track progress, such as the calendar view, which is more a high-level overview of the production cycle. But there are also customizable reports on project status, portfolio, variance and much more. All can be filtered to show only the data stakeholders want to see and shared with them across formats.
ProjectManager is online project and portfolio management software that connects teams whether they’re in the office or on the factory floor. They can share files, comment at the task level and stay updated with email and in-app notifications. Join teams from companies, such as Avis, Nestle and Siemens who are using our software to deliver success. Get started with ProjectManager today for free.