Manufacturing requires the right balance of many factors. One of the most important is inventory management—the materials and components needed for the manufacturing process. The more efficiently a company handles its material requirements, the more profit it will find. And material requirements planning or MRP helps manufacturing businesses and other organizations do that.
What Is Material Requirements Planning (MRP)?
Material requirements planning is a software-based method that uses an MRP system to help businesses manage their production inventory levels and supply chain. When used properly, MRP systems facilitate production planning, reduce manufacturing costs and improve productivity.
How Does MRP Work?
An MRP system uses several inputs to gather production planning data, such as the product’s bill of materials, master production schedule, production inventory levels and other data sources to calculate what materials are required and when.
Therefore, by telling you when materials are needed, an MRP system can help you avoid two common inventory control issues: overstocking your production inventory, running out of stock and delaying your production schedule.
ProjectManager is great for manufacturing companies. ProjectManager’s project management tools such as Gantt charts can help you map your production schedules and collaborate with your team in real time. This makes it easy to see when materials will be required, complementing MRP’s calculations. You can also track resources such as labor and materials with real-time dashboards and much more. Get started for free.
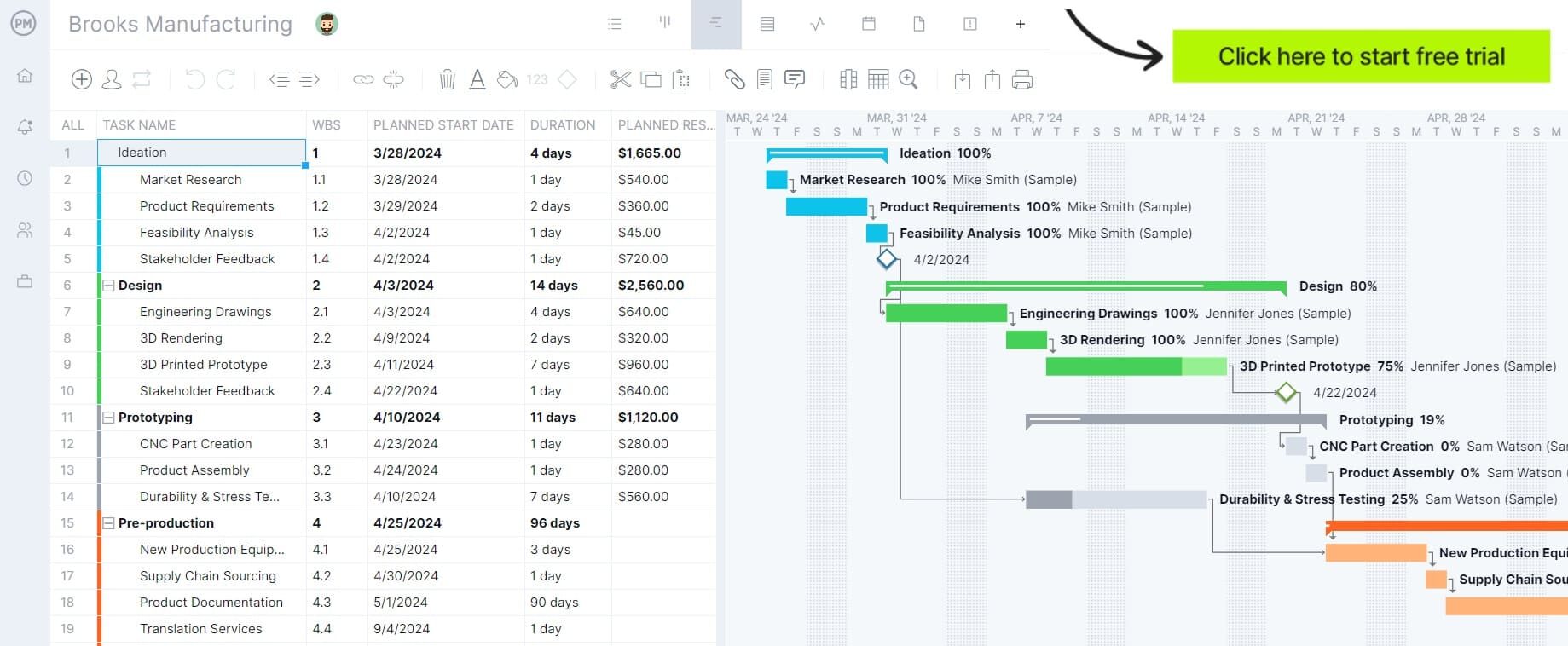
Manufacturing resource planning (MRP) is often confused with enterprise resource planning (ERP), a similar term, but their scopes are different.
MRP vs. ERP
ERP systems provide a single platform for all your enterprise information such as accounting, customer relationship management (CRM), manufacturing resource planning, warehousing and other types of data.
MRP systems, on the other hand, focus on production materials and rely heavily on the quality of their inputs to automatically calculate the material requirements of a business. Let’s learn more about these MRP inputs.
MRP Inputs
For a material requirements planning system to operate, there are three essential elements of material requirements planning. To better understand them, let’s take a look at each:
- MRP Information Sources: There are four key information sources that MRP systems use to make their calculations. These sources include production schedules, material specs, production cycle times and supplier lead times. Use these four data streams to adjust projection machinery and production process flows.
- Case Studies: Use research for greater business intelligence. Think about customer demand, inventory requirements, sales forecasts and other supply chain management considerations. This, in conjunction with feedback from other companies, can fill gaps in the MRP’s information sources. Then, the executives of the business must provide the right resources to apply the results of their research.
- Unavoidable Problems: Some issues won’t go away with automation and research. There are technical and operational problems that you can only solve through adequate training, support and information sharing. Once the master production schedule and material specs are decided on, labor must conform to these constraints before proceeding.
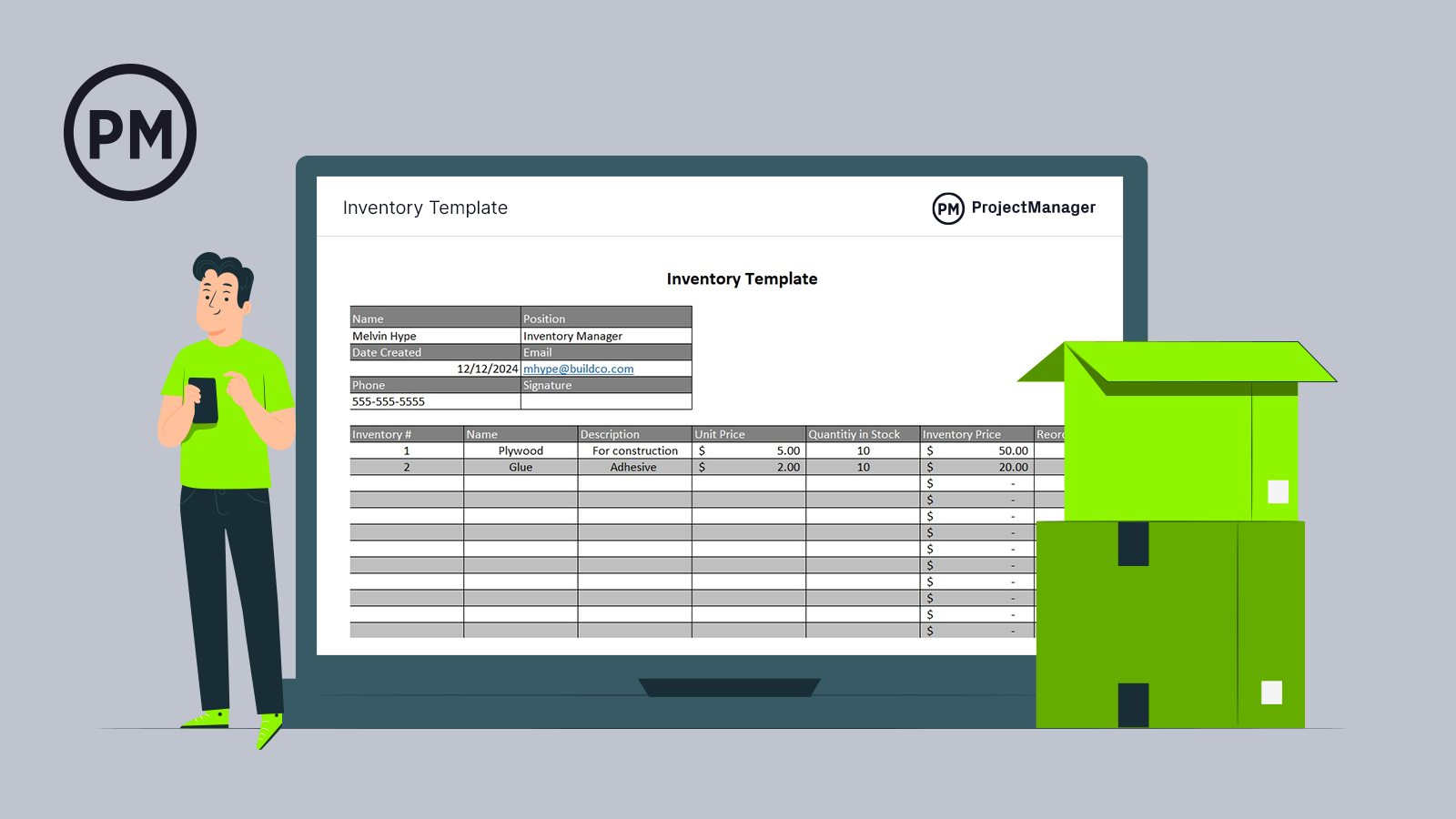
Get your free
Inventory Template
Use this free Inventory Template for Excel to manage your projects better.
MRP Outputs
Using the inputs explained above, an MRP system will calculate what materials are needed, how much material is needed, and when they should arrive.
Once you have this information, you can choose to implement just-in-time delivery (JIT), which consists in scheduling production as materials get to the production line. This helps organizations save on inventory costs, as materials don’t pile up in warehouses, but rather get to the facility directly for production.
MRP In Manufacturing
MRP is critical for manufacturing businesses. Material requirements planning helps manufacturers keep low production inventory levels because they’re controlling the manufacturing, purchasing and delivery activities. Before the advent of computers, production planning was all done by hand, using calculations for reorder quantity and reorder point.
Benefits of Using MRP
Using an MRP system keeps the raw materials and components for your product available when you need them while minimizing inventory levels. This reduces costs associated with stocking materials and ensures your company always has what it needs on hand.
Material requirements planning also helps with managing inventory more efficiently while reducing customer lead times. All this, of course, leads to an improvement in your production process. These factors all contribute to increased profits and customer satisfaction. However, that doesn’t mean using an MRP system is all rosy.
You need good data to get good results. Without good data, you’re going to miscalculate—and that can have devastating impacts on the business. Plus, using computer-based platforms that run MRP systems can be expensive to implement.
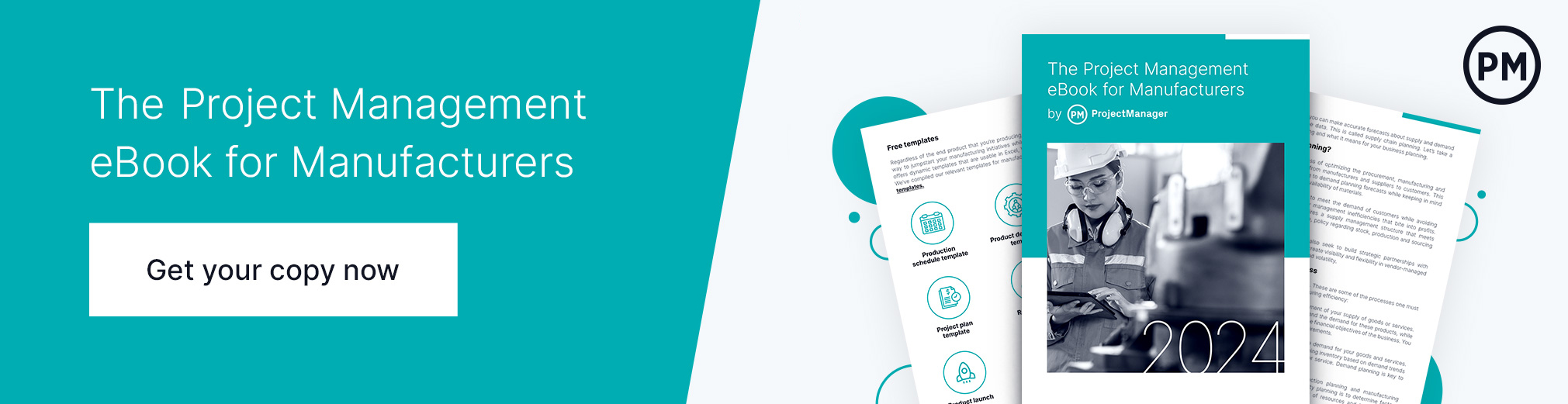
Disadvantages of MRP
The main disadvantage of MRP is that it depends on the accuracy of the data that is used, so the quote “bad data in, bad data out” can be true for many MRP systems.
If you’re using bad data for your MRP system, you could end up with an inaccurate production schedule, production inventory shortages, lost contracts and many other negative consequences, so if your inputs are not accurate, it’s better to avoid implementing MRP.
Inventory Template
This free inventory template for Excel is ideal for managing production inventories. It allows you to list all your inventory items, their inventory price and quantity in stock and reorder quantity, among other important details to help you maintain optimum production inventory levels.
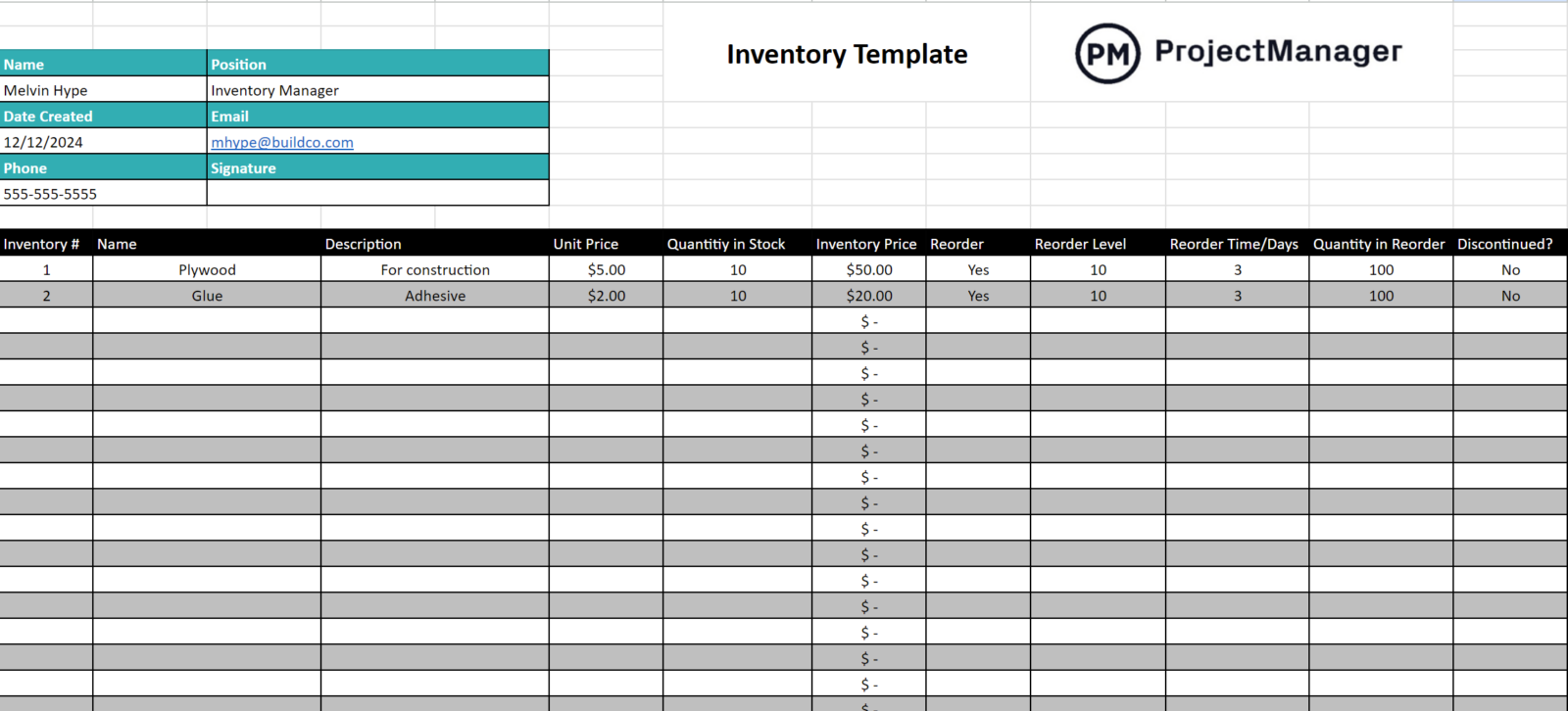
How ProjectManager Helps With MRP
Project management software can offer you the tools to monitor and track material requirements to make sure your supply is always in balance with demand. ProjectManager is a cloud-based software that provides managers with rich data to give them greater insight into their production process.
Create Production Plans on Gantt Charts
To organize your resources and timeline, use ProjectManager’s Gantt chart to create your production schedule. You can set up tasks, assign them, link dependent tasks and set milestones.
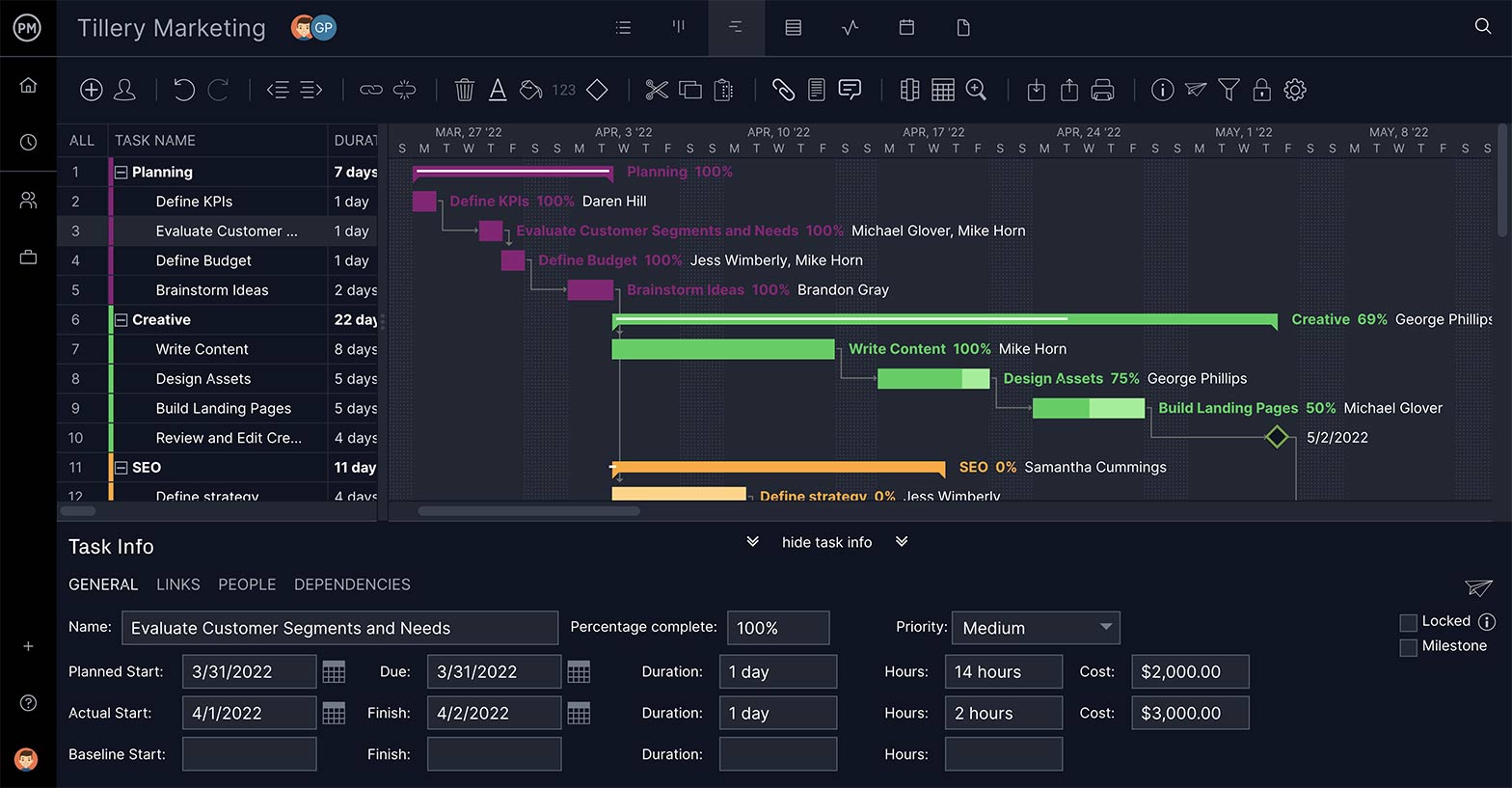
Ensure Your Resources Are Properly Allocated
To manage your resources, use the workload chart. It’s color-coded to show you how much work you have assigned to your team members. Then, from the workload chart, you can reallocate the assignments to balance your labor force and keep everyone productive.
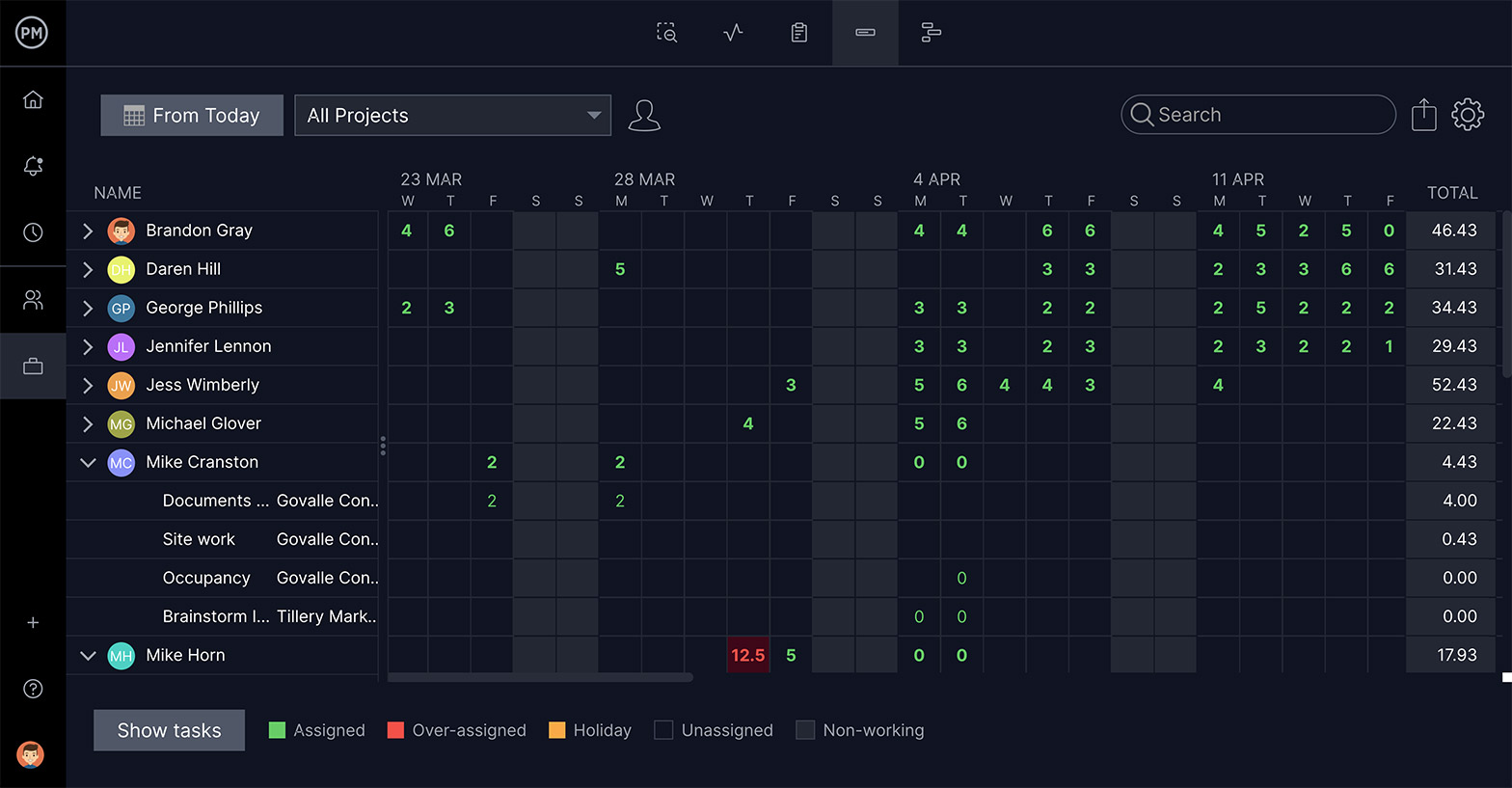
Monitor and Track Your Production Cycle
In terms of monitoring your production and resources, ProjectManager has two tools. The real-time dashboard collects live data and automatically makes calculations, which are displayed in easy-to-read charts and graphs. For more detail, use filterable one-click reports to show just the data you’re interested in. Then share them to keep stakeholders updated on progress.

An MRP system isn’t for everyone, especially if you can use ProjectManager. Our award-winning software helps you plan, monitor and report on production while managing resources to keep inventory low and meet demand. Kanban boards offer visibility into production so you can allocate resources to keep teams working at capacity. Try ProjectManager free today.