As with any project, manufacturers are working with the triple constraint of time, cost and scope. One constraint that’s often overlooked is quality. Products have to be safe and meet customer requirements, including quality. Having a control plan helps production achieve these goals.
To do this, manufacturers must understand what a control plan is, the different types of control plans and the steps to make a control plan for manufacturing. We’ll go over that, explain the benefits of a control plan and even link to a free control plan template to help you get started.
What Is a Control Plan?
A control plan is a document describing everything from measurements, inspections, quality checks or monitoring process parameters required at each phase of a process to ensure that the process outputs conform to the requirements. In other words, a control plan gives the operator or inspector the information needed to properly control the process and product quality parts or assemblies.
There are also instructions on what to do if non-conformance is detached. The control plan isn’t a replacement for detailed operator instructions, though in some cases it’s used with an inspection sheet or checklist. The goal of a control plan is to maintain quality in a process regardless of turnover in the workforce as it provides a standard for quality inspection and process monitoring. The control plan is a living document that’s periodically reviewed and updated as measurement methods and controls are improved over the product’s life cycle.
A control plan is more efficient when scheduled in project management software. ProjectManager is award-winning project and portfolio management software with Gantt charts and sheet views that can outline the control plan on a production schedule, share it with workers and monitor its progress in real time.
The Gantt chart shows the control plan on a timeline, while the sheet view is a Gantt chart without that timeline. Either way, managers can set up tasks for inspections, quality checks and more, make assignments and link all four types of task dependencies to avoid costly downtime. Once the schedule is done, set a baseline to monitor planned progress against actual progress in real time. Get started with ProjectManager today for free.
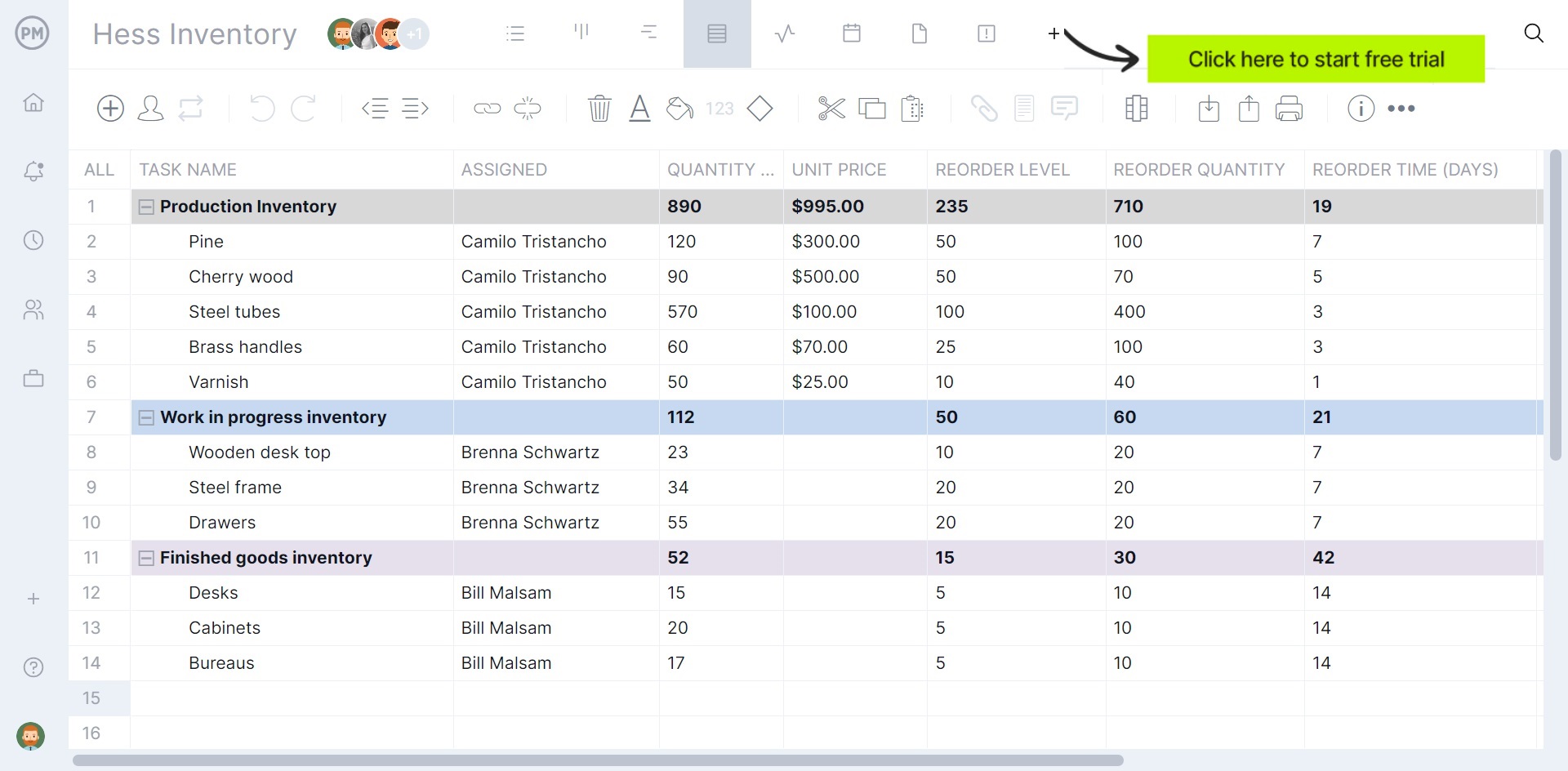
Types of Control Plans in Manufacturing
There isn’t one control plan as it’s broken down into three levels. It’s up to the production team to determine the proper level for the process being controlled. Those three levels for a control plan are based upon what point the product is at in the new production introduction (NPI) process. They are prototype, pre-launch and production. Let’s explain each below.
Prototype Control Plan
This level of a control plan will include a description of the dimensions that will be measured and the material and performance tests that will be completed during the prototype build. The prototype build is an early version of the product, but not yet the final product. It’s created to test the product’s functionality, features and design before going into mass production to identify incorrect or faulty parts and issues and to gather feedback from the target market.
Pre-Launch Control Plan
The pre-launch control plan level will contain descriptions of the dimensions measured and the material and performance tests to be completed after the prototype but before the product launch and regular production. This improves quality assurance through increased controls and includes all known criticalities of the product and process, increased quality checks and frequency, etc.
Production Control Plan
The last control plan level is production. This level contains a comprehensive listing of the product and process special characteristics, the process controls, measurement methods and tests that will be performed during regular production. It lists all the steps for the entire production of the product and, as mentioned above, is a living document that’s reviewed and updated as needed.
Get your free
Control Plan Template
Use this free Control Plan Template for Excel to manage your projects better.
How to Make a Control Plan for Manufacturing
When making a control plan for manufacturing, there are seven basic steps developed by cross-functional teams that understand the process being controlled and can identify more opportunities for improvement than a team dedicated to only one manufacturing aspect.
Though there’s a control plan template, a form that captures the pertinent information in a control plan, the control plan is more than just that. The team develops it to control the process and ensure the product quality meets customer expectations. The following seven steps capture the process of developing a control plan for manufacturing.
1. Gather Information About the Supplier
The supplier will provide the raw materials needed to produce the product. Therefore, the manufacturer should gather information about the supplier, including financial statements, certifications, quality control processes, insurance coverage, business continuity plans, risk management practices and their ability to handle potential disruptions. Manufacturers must be certain that their suppliers can provide them with what they need and when they need it.
2. Describe the Part or Process That Will Be Inspected in Detail
List the part or process number, its name and description, thoroughly describing each process step and what it accomplishes. List any special tools or machines used to carry out the process step. The inputs that influence the outputs or product characteristics should also be detailed, such as ambient temperature, weld torch temperature, bolt torque, etc.
3. Determine What Aspects of the Part or Process Will Be Inspected
Your organization might employ industrial processes such as molding, cutting, casting and CNC machining, among others. For each of these processes, various aspects might be subject to a quality control inspection.
For example, if you’re a manufacturer making steel rods for construction, you’ll need to do a casting process. You might want to check various aspects once this particular process is completed such as the stress resistance, density, diameter and other quality control aspects of the casted steel rods. You should include each of these aspects in your control plan. The more you add, the more thorough it will be.
4. Establish a Measurement Technique
Identify the tools that will be used to make measurements, such as gauges, fixtures, test equipment and others that can evaluate the process or part specification. It’s recommended that a measurement systems analysis (MSA) is used to ensure that the correct, consistent usable data is being collected.
5. Determine the Sample Size and Inspection Frequency
Determining what the sample size is for inspection is an important part of any empirical study. The sample size is usually based on the cost, time or convenience of collecting the data and the need for it to offer sufficient statistical power. In terms of the frequency of the inspection, consider such factors as administrative agency policies and guidelines, possible risk of work environments, operations and equipment used, number or worker shifts, etc.
6. Define a Control Method
Describe how the operation will be controlled, based on the strategy and analysis of the manufacturing process, the type of process and the risks found during quality planning. This is an important part of the control plan and must be reviewed and updated regularly.
7. Plan Future Actions if Needed
To determine if and what future actions are needed, analyze deviations when standards are not being met and understand why this is happening so it can be resolved. Use SMART goals to build the action plan. Prioritize activities by considering the potential impact of each activity. Then create a timeline with start and finish dates and planned hours for each task. Finally, see if the action plan worked or if the problem returns. If it does, then start again to discover the root cause.
Control Plan Template
This free control plan template for Excel is a quality management tool that can help you keep track of the quality of the output of all the different manufacturing processes that your organization employs for manufacturing products.
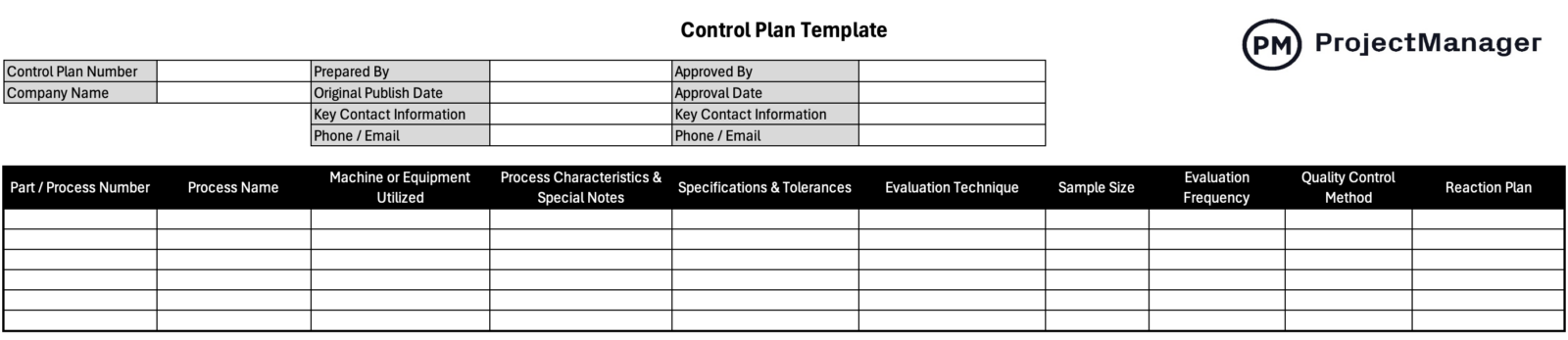
Benefits of Having a Control Plan
Having a control plan prevents scrambling to respond to issues in production. By having a control plan, those anomalies can be discovered early enough so they lessen the impact on cost and time. Here are some of the improvements of taking the time to develop a control plan for manufacturing.
- Improves quality, preventing nonconforming products, identifying, managing and reducing variations, scrap and rework
- Improves efficiency and costs by reducing waste, improving throughput without sacrificing quality
- Improves customer satisfaction, focuses on what’s important to the customer and organization and keeps poor quality products from reaching customers
- Improves process management by having a plan for responding to change, communicates changes in production and process, has a control method and measurement methodology, monitors processes to ensure improvements are maintained, employs prevention rather than detection
More Free Manufacturing & Production Templates
Download more free templates for Word, Excel and in-app project templates to help manage projects from start to finish. There are over 100 free templates, many of which are industry-specific. Here are a few related to manufacturing and production.
Standard Operating Procedure Template
A standard operating procedure (SOP) is instructions on how to execute a task or process. Use this free standard operating procedure template for Excel to ensure that production is done properly and everyone on the manufacturing floor is clear on the process.
Production Schedule Template
For those without project management software, a free production schedule template for Excel can help them balance supply and demand when producing commodities. This free template is built to be flexible enough to respond to fluctuations in demand and set up inventory to avoid stockouts.
A bill of materials lists what’s needed to assemble a product, but also acts as an instruction manual, which helps manufacturers plan the materials they need for production. Use this free bill of materials template for Excel to help estimate, plan and control inventory, avoiding delays and waste.
ProjectManager Helps Manage Manufacturing Projects
Using templates for production and manufacturing processes is not the best way to work efficiently. These static documents pull managers and their employees away from production to manually update the templates, which is not the best way to use workers’ time. Templates are also poor collaborative tools. Project management software rights those wrongs. ProjectManager is award-winning project and portfolio management software that can make flexible production schedules that managers can use to monitor work in real time, assign tasks to teams and manage resource allocation to boost productivity and reduce waste.
Assign Tasks to Team Members and Track Their Progress
Managers can assign tasks from the Gantt chart and teams can manage their work on one of the multiple project views. They can use robust task lists that track progress and more or visualize their workflow on kanban boards that also track progress, costs and more. Managers get a high-level overview of the team’s progress on real-time dashboards that automatically capture live data and display it in easy-to–read graphs and charts on time, cost, tasks, workload and more. Customizable reports go deeper into the data and can be shared to keep stakeholders informed.

Manage Resources and Monitor Costs
Before assigning the team, when onboarding them managers can set their availability. Now, when making assignments, it’s easy to see who’s on vacation, has PTO and what day global holidays fall on. Managers can view the color-coded workload chart or team page to get an overview of everyone’s allocation. From there, they can balance their team’s workload to keep them working at capacity and boost productivity. Labor costs can be monitored on dashboards, status, portfolio or timesheet reports. Timesheets give managers visibility into each team member’s progress on their tasks and how much it’s costing.

Related Quality Management Content
A control plan is only one aspect of the larger quality management activities that manufacturers and other professionals employ to meet customer requirements. For those who want to go deeper into the subject, below are a few pieces recently published on quality assurance, planning and more.
- Project Quality Management: A Quick Guide
- The Quality Assurance Process: Roles, Methods & Tools
- The Quality Management Plan in Project Management
- What Is Quality Planning & Why Is It Important?
ProjectManager is online project and portfolio management software that connects teams whether they’re in the office, on the factory floor or anywhere in between. These can share files, comment at the task level and stay updated with email and in-app notifications. Join teams at Avis, Nestle and Siemens who use our software to deliver successful projects. Get started with ProjectManager today for free.