Businesses are always looking for ways to improve efficiency. Manufacturers are no different, except in the areas in which they seek to standardize and streamline their production processes. One method they use is shop floor manufacturing.
For those new to the term, let’s first define its parts, such as what is a shop floor and a shop floor plan. Then we’ll explore shop floor management, what a shop floor manager does and best practices to achieve the benefits of effective shop floor management.
What Is a Shop Floor?
Before understanding shop floor management, it’s important to know what a shop floor is. A shop floor is where the production is done. It’s that area of the factory or working place where the employees produce goods.
What Is a Shop Floor Plan?
A shop floor plan is used to manage the activities that happen or are related to the shop floor. That includes the management of operations planning, inventory, equipment and workers. It is part of the larger shop floor management, which we’ll get into next.
What Is Shop Floor Management?
Shop floor management is a methodical approach to the management and supervision of all the activities that are related to the shop floor. That means organizing all the tasks assigned to the workers in the factory, coordinating their workflows and ensuring that production goes smoothly in the production chain.
The goal of shop floor management is to standardize and streamline the processes that are taking place in and around the shop floor, reduce waste and increase the output of production without jeopardizing the quality of the products being produced or the safety of the employees that are making them.
One way to ensure that these goals are achieved is through project management software. ProjectManager is award-winning project and portfolio management software that can create dynamic production schedules with multiple tools. Production managers can organize tasks, link dependencies and set a baseline to track actual progress against planned progress in real time on Gantt charts or the sheet view. Workers can see the schedule without getting into the weeds so they can focus on their tasks with kanban boards or task lists. Stakeholders can get an overview of the production schedule on the calendar view. Get started with ProjectManager today for free.
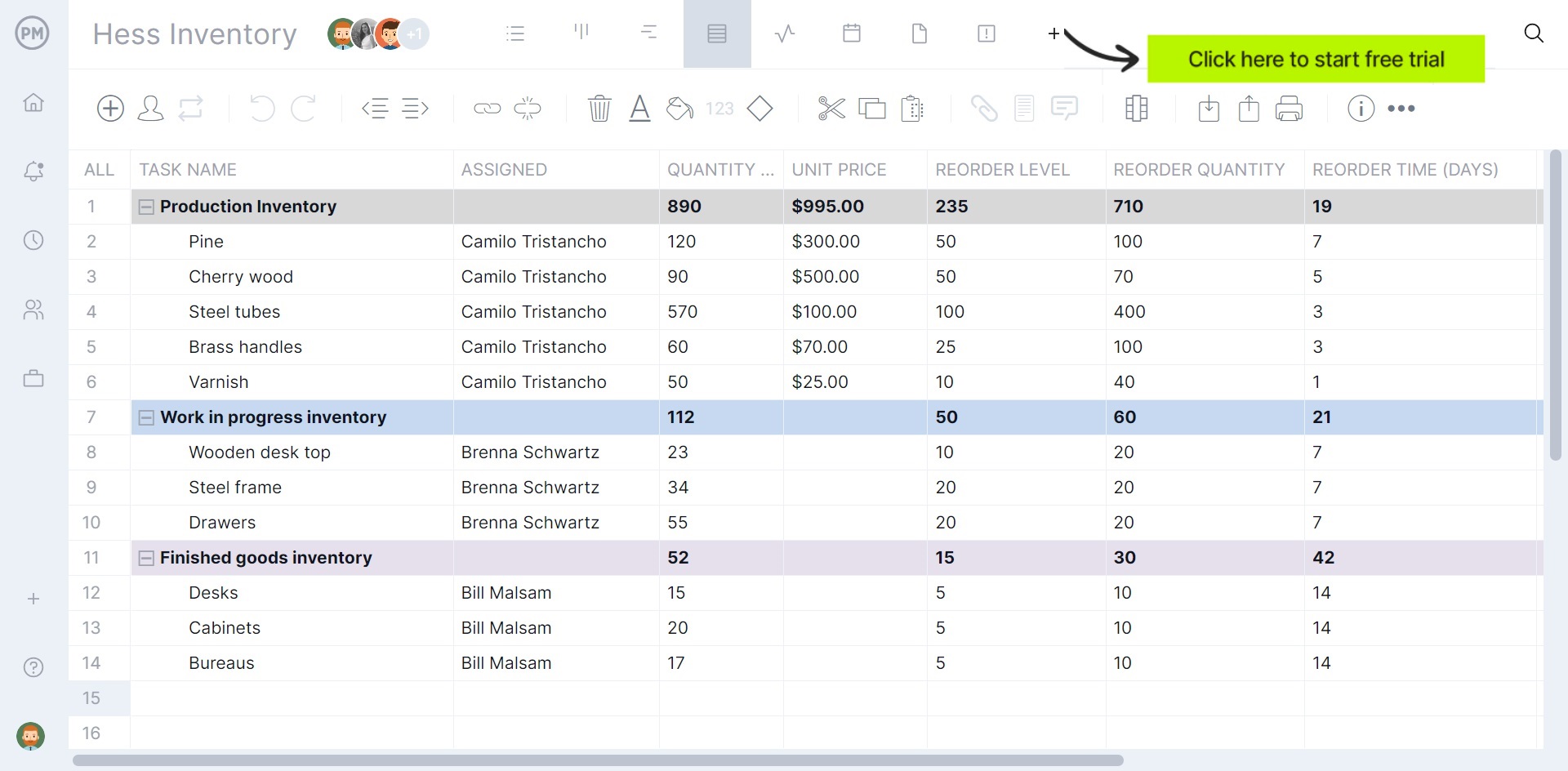
The shop floor management process has three basic phases, shop floor planning, scheduling and control.
Shop Floor Planning
This step involves the creation of the master production schedule, which informs which manufacturing orders will be made. Next, the order release document will tell the shop floor management boards the resources and manufacturing processes used to create the order.
Shop Floor Scheduling
Shop floor applications are now scheduled for the production of the order. A detailed workflow of the manufacturing route that the order will go through and a bill of materials are also created. This phase explains the workstations the order passes through and the materials and quantities needed for the order. This schedule allows managers and workers to understand what needs to be done, who needs to do it and how it needs to be done.
Shop Floor Control
Shop floor scheduling boards monitor the progress of the manufacturing order and other production operations to ensure they’re going as planned. Through software and other tools, the production orders are managed, progress tracked, resources optimized and risks mitigated. This enhances efficiency through the use of real-time data monitoring and automation.
The Role of a Shop Floor Manager
A shop floor manager is responsible for the factory floor or work area which is a very important area of production management. They ensure that all the various departments in the manufacturing business are running smoothly, effectively and safely.
The shop floor manager has many responsibilities, including driving sales, enforcing company policies, ensuring that products meet merchandising standards, complying with safety regulations and also some financial administration and site management responsibilities.
Because the shop floor manager executes the operations done on the factory floor, they’re an essential part of shop floor management. They create the processes, methods and systems to ensure production is as efficient as possible.
Capacity Planning Template
A tool that every shop floor manager needs to execute shop floor management is a capacity plan. Capacity planning determines how much production capacity is needed to meet the demand for the product.

Download this free capacity planning template for Excel to reduce stockouts and identify inefficiencies in your manufacturing processes to increase delivery capacity. By understanding the resource capacity of your company, it’s easier to create a production plan that can meet future resource requirements.
Shop Floor Management Best Practices
There are several ways to improve shop floor management to ensure that inefficiencies are reduced and production increases without sacrificing quality. Below are several best practices to employ when implementing shop floor management.
Implement the 5S Method From Lean Manufacturing
The 5s method used in lean manufacturing is a methodology for organizing, cleaning, developing and sustaining a productive work environment. The definitions of those five pillars of the practice are described below.
- Sort (Seiri): Sorting items and materials, removing anything unnecessary to reduce lost time and distractions and increase usable space and safety.
- Set in Order (Seiton): Puts all necessary items in the best place to make a business’ workflow operate smoothly and efficiently.
- Shine (Seiso): Keep the workspace, tools and machinery clean and remove any source of contamination to make it safe and easy to work in.
- Standardize (Seiketsu): The process of maintaining the first three Ss and implementing procedures and schedules that reinforce those steps.
- Sustain (Shitsuke): Trian, educate and change habits while following the first four steps to enforce the entire methodology.
Use Visual Management Tools & Techniques
These are used to impart information quickly to teams during the daily, weekly or monthly meetings or as they execute their tasks. Some of the most commonly used ones are described below.
- Kanban Boards: A physical or digital tool that visualizes work, limits work-in-progress and maximizes efficiency.
- Flowcharts: A diagram that shows a process, system or computer algorithm to communicate complex processes in a clear, easy-to-understand way.
- PERT charts: A program evaluation review technique chart graphically represents a project timeline and the tasks needed to complete it.
- Gantt charts: Illustrations work completed over a period about the time planned for that work on both a spreadsheet and timeline.
- Andon Systems: Used to quickly alert operators about a problem on the line to help resolve the problem and get the assembly line back to normal operation.
Establish Manufacturing KPIs
Shop floor management monitors and controls the activities that occur in the working area of a factory. To do this, a shop floor manager must first have well-defined and quantifiable metrics to measure the work to ensure it’s on schedule and within budget. Some common manufacturing KPIs include throughput (production capabilities of a machine, line or plant), cycle time (the average amount of time it takes to produce a product), demand forecasting (amount of raw materials required to meet future demand) and many more.
Clearly Define Standard Operating Procedures
Standard operating procedure is a document that helps operators navigate their daily tasks with clarity and precision. The goal of using a standard operating procedure is to structure and standardize how work is done, leading to greater efficiency and productivity.
Benefits of Effective Shop Floor Management
There wouldn’t be shop floor management if there were advantages for manufacturers employing it. Here are several of those benefits.
Eliminate Waste from the Manufacturing Process
Shop floor management strives to remove various forms of waste, such as overproduction, excess inventory, unnecessary movement, waiting time, defects and overprocessing, from the manufacturing process. This leads to greater efficiency and productivity.
Improve Your Overall Equipment Effectiveness (OEE)
Overall equipment effectiveness is the measurement of manufacturing productivity. It identifies the percentage of manufacturing time that is truly productive. The goal is to have a score of 100 percent, which means production is moving as fast as possible with no stop time.
Optimize Production Routing and Assembly Line Balancing
Optimizing production routing and assembly line balancing arranges the individual processing and assembly tasks at the workstations. This helps balance the total time required at each workstation. This results in greater productivity, savings in time and production costs.
Facilitates Production Control
Integrate real-time data from various stages of the manufacturing process to enable a comprehensive understanding of current market trends and customer needs, which helps demand forecasting. In terms of production, it compares the target data of production planning with the actual data and if a deviation works to resolve the problem.
More Free Templates for Production and Manufacturing
Many templates can help in shop floor management. Download over 100 free project management templates for Excel and Word from our site. These free templates cover all phases of a project across many industries. Below are a few that address production and manufacturing.
Bill of Materials Template
A bill of materials lists what’s needed to create a product. But more than just a list of materials it documents how to assemble those pieces into a finished product. Use this free bill of materials template for Excel to list the quantity and cost of those materials, plus the procurement process, assemblage and repair, if needed.
Maintenance Schedule Template
Factory machinery has to be in good working order or production will suffer an unplanned shutdown. This free maintenance schedule template for Excel can be used regularly to schedule the frequency of maintenance to avoid breakdowns or worse, which can negatively affect schedules, budgets and customer satisfaction.
Standard Operating Procedure Template
We mentioned the importance of a standard operating procedure above. This free standard operating procedure template for Word captures all the information necessary to direct your production team on how to do their tasks. This helps increase productivity and consistency but also ensures legal compliance.
Manage Your Shop Floor With ProjectManager
All these free production and manufacturing templates are useful, some more than others, but none of them are going to help manage production resources, track costs or balance a team’s workload. To go beyond what templates can provide requires using project management software. ProjectManager is award-winning project and portfolio management software that collects live data for shop floor managers to make more insightful decisions. We’ve already shown how we can schedule production line activities and have workers execute their tasks on tools that help them work more efficiently. Here are some other ways we can help with shop floor management.
Manage Resources & Track Costs
The first step in managing resources is knowing their availability. When onboarding production workers, set their vacation time, PTO and even global holidays and it’s easy to see who is free to work when. To track labor costs, either toggle over to the real-time dashboard or portfolio dashboard for an overview of project costs, but also time, workload and more.
There are status, portfolio, variance and other reports that can give shop floor managers more detail. They can also view secure timesheets, which streamline payroll and help track labor costs by providing visibility into how far each team member is in completing their tasks.

Balance the Team’s Workload
Once team members are assigned, go to the color-coded workload page or the team page for an overview of everyone’s allocation. From there, production managers can balance their workload to keep everyone working at capacity and staying productive. Custom workflows can be created for the team and even automated to relieve them of small, repetitive tasks. Managers can set up triggers that produce actions, such as changing the status of a task or who’s assigned to it. To ensure that quality standards are met, task approval settings can be made to oversee the process.

Related Production and Manufacturing Content
There’s more to manufacturing than shop floor management. For those interested in learning more about manufacturing operations management and production planning or downloading more free manufacturing templates, follow the links below.
- 14 Free Manufacturing Excel Templates
- Manufacturing Operations Management Explained
- Production Planning 101: Making a Production Plan (Example Included)
- Production Control: Process, Types and Best Practices
- How to Calculate Production Capacity: Formula & Examples
ProjectManager is online project and portfolio management software that connects teams whether they’re in the office, on the factory floor or anywhere else. They can share files, comment at the task level and stay updated with email and in-app notifications. Join teams at Avis, Nestle and Siemens who use our software to deliver success. Get started with ProjectManager today for free.