Construction project management is designed to deliver projects on time and on budget while maintaining or improving quality. Value engineering in construction is one method general contractors use to achieve those goals.
What is value engineering in construction? We’ll answer that question and show how to implement it through various techniques. Then it’ll become apparent why this benefits anyone involved in construction projects.
What Is Value Engineering in Construction?
Value engineering in construction is a systematic method aimed at improving the value of a project by optimizing its function while reducing costs. It involves analyzing project components, processes and materials to find the most efficient and cost-effective solutions without compromising quality, safety or performance.
The goal of value engineering is to maximize the return on investment (ROI) by identifying unnecessary costs and eliminating them through alternative approaches. This process typically occurs during the design phase, but can also be applied during construction to find more economical methods.
Value engineering in construction works by function analysis, which identifies the essential functions of a project component. It then applies cost reduction by finding less expensive materials or construction methods without sacrificing quality. This involves creative problem solving to find innovative solutions to meet project objectives by collaborating with stakeholders, designers, engineers and contractors.
Project management software can help with value engineering in construction. These tools have a suite of features that can support cost control, resource management and project optimization throughout the project lifecycle.
ProjectManager is award-winning construction project management software with budget and cost management tools. Gantt charts can schedule tasks, resources and costs, helping construction managers identify areas where costs can be reduced without affecting the project’s quality or performance. More than that, our Gantt charts link all four types of task dependencies to avoid cost overruns, filter for the critical path to manage slack and can set a baseline to monitor expenditures in real time to spot inefficiencies early for better decision making for cost reduction. Get started with ProjectManager today for free.
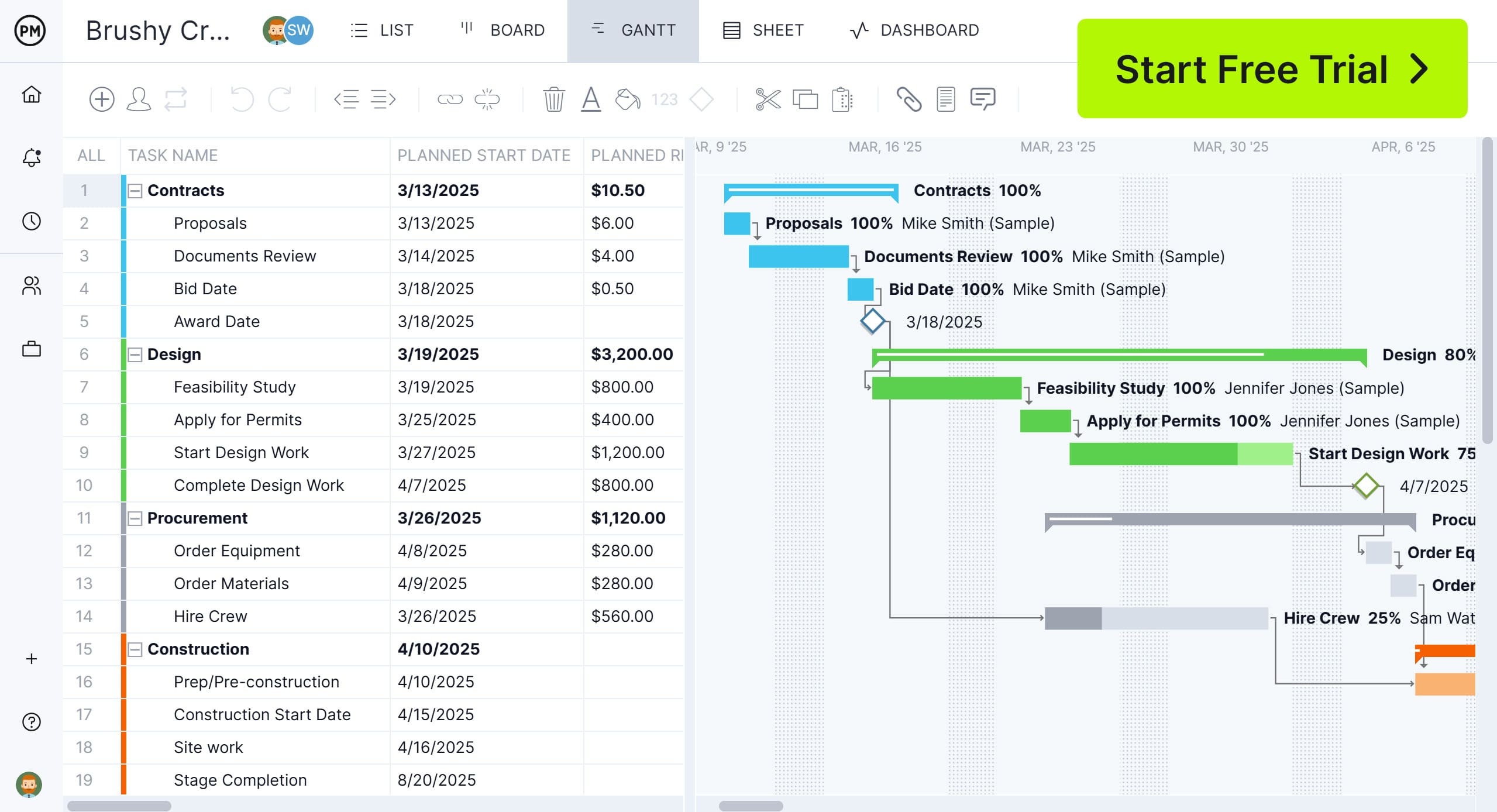
How to Implement Value Engineering in Construction
Implementing value engineering in construction is a systematic process aimed at optimizing a project’s value by balancing function and cost. The goal is to achieve the best possible outcome by identifying cost-effective alternatives without sacrificing quality or performance. This approach is typically employed during the design and planning stages, but can also be applied during construction to identify and implement efficiencies.
The process of value engineering follows a structured methodology divided into distinct phases. These phases guide the team in analyzing and improving the project in terms of function, cost and feasibility. Here are the key phases in implementing value engineering in construction.
Information Phase
In the information phase, the project team gathers all necessary data and documentation related to the project, including specifications, design plans and budget information. This phase focuses on understanding the project’s scope, objectives and constraints, providing a clear picture of the current state before any changes are made. The more comprehensive the data collected in this phase, the better the analysis and decision-making in later stages.
Function Analysis Phase
During the function analysis phase, the project team identifies and defines the essential functions of each component or aspect of the project. This phase helps to understand what the project needs to achieve and the core functions of each item or process. By breaking down each function and its associated costs, the team can determine where value improvements or cost savings can be made without affecting the project’s overall performance.
Creative Phase
The creative phase is where the team brainstorms and explores all possible alternatives or innovative solutions to achieve the same functions more efficiently or cost-effectively. No idea is off-limits during this phase, and the focus is on creativity and problem-solving. The team can propose different materials, processes, technologies or design modifications that can help lower costs while still delivering the intended outcomes.
Evaluation Phase
In the evaluation phase, the ideas and alternatives generated during the creative phase are reviewed and assessed based on their feasibility, cost-effectiveness and impact on the project. This phase involves conducting a detailed analysis to determine which alternatives offer the greatest value for the lowest cost. Criteria such as performance, risk and implementation time are weighed against the potential savings or benefits.
Development Phase
After evaluating the alternatives, the most promising options are taken forward for further development in the development phase. This phase involves creating more detailed plans and specifications for the selected alternatives, determining their practicality and cost implications. It may also involve testing or prototyping to ensure the proposed changes can be successfully integrated into the project.
Presentation Phase
In the presentation phase, the developed ideas and alternatives are presented to the project stakeholders, such as clients, designers, contractors and team members. This is where the final recommendations are made, showcasing the benefits of the proposed changes and justifying the cost savings and value improvements. The goal is to get approval from stakeholders for the proposed value engineering solutions.
Implementation and Follow-Up Phase
Finally, in the implementation and follow-up phase, the approved value engineering recommendations are put into action. This phase includes integrating the changes into the project’s design or construction process. It’s critical to monitor the progress and effectiveness of the implemented changes. The project team should track outcomes, compare actual savings with projected savings and ensure that the improvements are properly incorporated into the project, ensuring long-term success.
Techniques for Value Engineering in Construction
Value engineering in construction relies on structured techniques to optimize costs while maintaining or improving a project’s functionality and quality. These techniques help project teams analyze design, materials and processes to find the most efficient solutions. Below are some of the most effective techniques used in value engineering for construction projects.
1. Target Value Design (TVD)
Target value design is a cost-driven approach that aligns project design with a predetermined budget. Instead of designing first and then estimating costs, TVD ensures that designs are developed with cost constraints in mind from the beginning. This method encourages collaboration among architects, engineers and contractors to create cost-effective solutions while maintaining project objectives.
2. Life Cycle Costing (LCC)
Life cycle costing evaluates the total cost of ownership of a building or infrastructure over its entire lifespan, rather than just considering initial construction costs. This technique factors in maintenance, operation, energy consumption and disposal costs to ensure that design choices lead to long-term savings. By prioritizing durable and efficient materials or systems, LCC helps maximize project value over time.
3. Function Analysis System Technique (FAST)
The function analysis system technique is a structured method used to break down a project or system into its core functions. It helps teams analyze how different components contribute to the overall project goal and identify areas where costs can be reduced without sacrificing essential functions. By organizing functions in a logical diagram, FAST facilitates better decision-making in value engineering.
4. Integrated Project Delivery (IPD)
Integrated project delivery is a collaborative approach that brings together all key project stakeholders—including owners, designers, engineers and contractors—early in the process to optimize design, cost and execution. By promoting teamwork and shared responsibility, IPD helps minimize waste, reduce costs and ensure that value engineering decisions are implemented effectively.
5. Design-to-Cost (DTC)
Design-to-cost is a method where cost targets guide the design process. Instead of allowing costs to escalate as designs become more complex, DTC ensures that financial constraints are considered from the start. This technique prioritizes value-driven decision-making by selecting materials, construction methods and designs that align with budgetary goals without compromising performance.
Benefits of Implementing Value Engineering in Construction
Value engineering in construction provides a structured approach to optimizing project costs and improving efficiency while maintaining or enhancing quality. By focusing on functionality and cost-effectiveness, value engineering helps stakeholders align project goals with financial constraints, leading to better project outcomes. Below are some key benefits of implementing value engineering in construction projects.
Helps Establish Realistic Stakeholder Expectations
One of the significant benefits of value engineering is that it aligns stakeholder expectations with project feasibility. By analyzing costs, functions and design alternatives early in the project, it ensures that all parties—owners, designers and contractors—have a clear understanding of what can be achieved within budgetary and time constraints. This transparency reduces misunderstandings and helps stakeholders make informed decisions about project scope and priorities.
Maximizes the Profit Margin for Contractors
Value engineering in construction helps contractors improve profitability by identifying cost-saving opportunities without sacrificing project quality. By selecting more efficient materials, alternative construction methods or streamlined processes, contractors can reduce unnecessary expenses and increase efficiency. Additionally, it can lead to reduced waste, shorter project timelines and better resource allocation, all of which contribute to higher profit margins.
Helps Define Clear Project Requirements and Construction Specifications
Through a structured function analysis, value engineering in construction ensures that project requirements and specifications are well-defined before construction begins. This clarity helps prevent design changes, delays and cost overruns later in the project. By focusing on the essential functions of each project component, it helps establish precise specifications that meet both performance and budgetary goals, leading to smoother project execution.
How ProjectManager Helps Manage Construction Projects
There are many ways in which ProjectManager can help with value engineering in construction. However, that’s only the beginning of how our award-winning project and portfolio management software can manage construction projects. We’ve already shown how our Gantt charts work, but they also adjust schedules and workflows for efficiency, optimizing the project timeline through better sequencing of tasks to reduce time and cost. We also have collaborative features, such as document sharing and commenting at the task level, which improve communication and teamwork are essential to identifying cost-effective solutions. But there’s more.
Allocate and Optimize Resources
Keeping costs down requires strict resource management. That begins with scheduling resources and costs on the Gantt chart to allocate labor, equipment and materials efficiently, but continues when onboarding teams. At that point, general contractors can set the team’s availability, including PTO, vacation and global holidays, which makes it easier to assign the right person to the right task at the right time.
Construction managers can analyze resource allocation by visiting the color-coded workload page and seeing who is overallocated or underutilized. They can then balance the team’s workload without leaving the chart. The team page gives a weekly or daily view of the team’s activities. It can be filtered by progress or priority and tasks updated right from that page to reduce waste by ensuring resources are optimally used.

Get Actionable Insights From Real-Time Dashboards and Reports
Managing construction projects and keeping costs aligned with the project budget requires monitoring and control. For a high-level overview, toggle over to the project or portfolio dashboards. There’s no setup required to view easy-to-understand graphs and charts on time, cost, workload and more. For more details on project performance, use customizable reports on project or portfolio status, variance, timesheets, workload and more. These reports can be filtered to evaluate potential changes to improve the project’s value or provide progress reports to keep stakeholders informed. Even our secure timesheets help by tracking labor costs to keep to the budget.

Related Content
Value engineering in construction is one way general contractors control costs when managing projects. There are other ways, too, of course. For those who want to delve a little deeper into the subject, below are a handful of links to recently published articles from our blog.
- A Quick Guide to Value Engineering for Projects
- Construction Quality Control: Essential Tips
- Construction Cost Management
- 10 Types of Construction Projects with Examples
- Construction Budget: A Quick Guide (with Examples)
ProjectManager is online construction project management software that connects teams whether they’re in the office or on the job site. They can share files, comment at the task level and stay updated with email and in-app notifications. Get started with ProjectManager today for free.