The best things in life are free, but manufacturing goods cost money. The cost of production of those products isn’t as straightforward as it might seem. The sum total investment that it takes for a business to create a good or service can be surprising.
Let’s take a closer look at the cost of production, what types there are and how to measure the cost of production. Then we’ll expand upon the definition with an example to better illustrate the definition. Finally, learn how project management software can track the cost of production to help you control it in your production line.
Free Capacity Planning Template
To stay on top of your production costs, you need to stick to a tight schedule and carefully manage your resources. Use our capacity planning template to allocate resources, track availability, calculate resource utilization and monitor labor costs. Download it for free today.

What Is Cost of Production?
Cost of production reflects all the costs that a business pays that are associated with manufacturing a product or providing a service. These costs include both direct and indirect business costs; direct costs are connected to the product, while indirect costs involve the maintenance and running of the company.
We’ll get into more detail about the types of production costs below, but in general, they can be many. Some costs of production are labor, raw materials, consumable manufacturing supplies and overhead. Any costs that a company incurs when manufacturing its products or providing its service that will create revenue for that company can be considered a cost of production.
Naturally, any business that makes something or delivers a service wants to know its cost of production. To ignore it is to risk the financial health of a company. For example, if the cost of production is always higher than the profits that a company brings in, that product or service must be discontinued to keep within budget. One way to track these expenses is with project management software.
ProjectManager is award-winning project management software that can help you plan, manage and track your cost of production. Use Gantt charts to plan production, including all costs related to executing that work. You can assign resources and other costs to individual tasks and then set a baseline to track planned costs against actual costs in real time. Now you always know if you’re keeping to your budget or not. Get started with ProjectManager today for free.
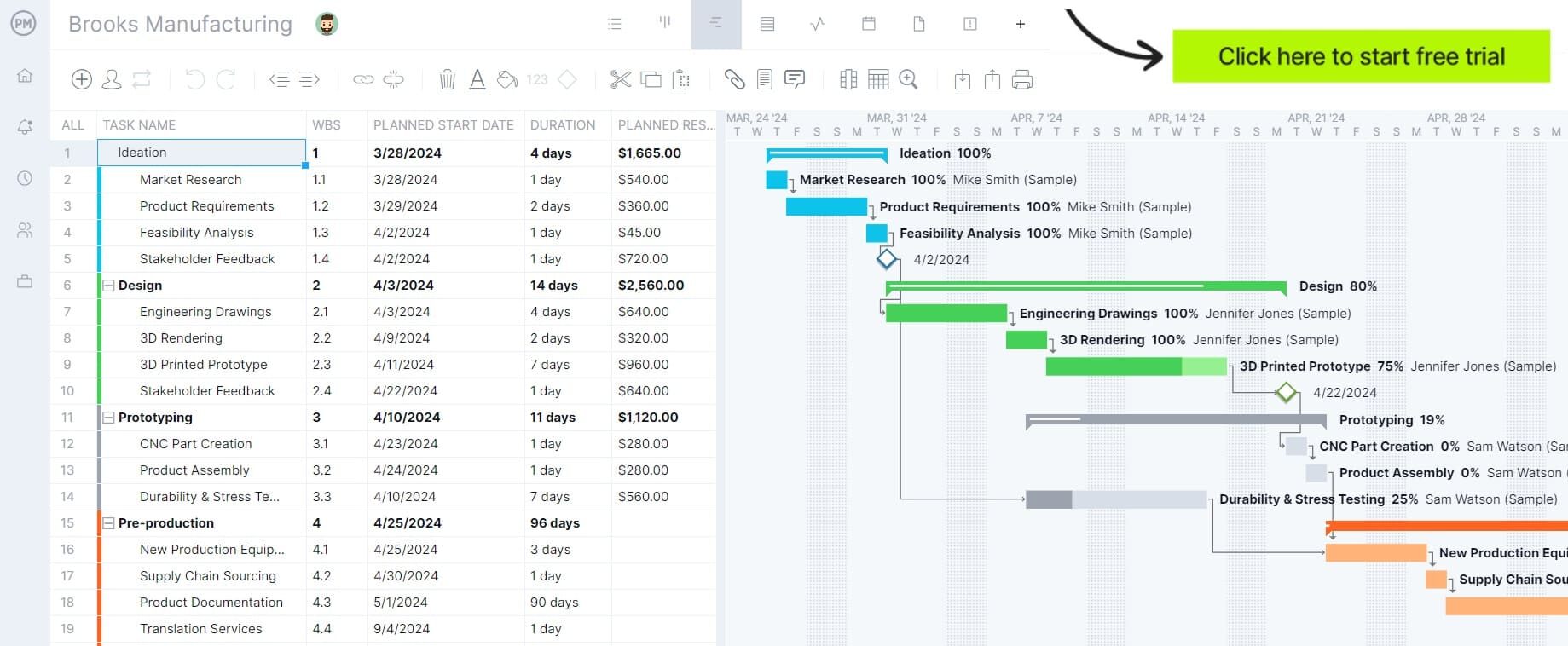
How to Measure Production Costs
To plan and manage the production costs, you need a way to measure them. Even before you start to manufacture a product or produce a service, it’s important to figure out what it’s going to cost. That way, you know how much the project is going to cost, which informs if you initiate the project or pass on it. Put another way, being able to calculate the cost of production helps you estimate your net profit or net loss on sales. That informs the retail price you put on the product and shows how high you can go without alienating your customers or negatively impacting your profits.
To figure out what the cost of production is, you need to add all direct and indirect costs of a manufacturing unit and divide that number by the total units produced. Whatever sum you arrive at, after adding all the production costs (a list of the different types we’ll get to in the next section), and dividing it by how many units you make, that’s your production costs. From there, you can make decisions about production management, pricing and more.
Types of Production Costs
Depending on your business and industry, there are many different types of production costs that you must be aware of to know how much of an investment the manufacturing of a product or development of a service will cost your company. We’ve boiled it down to what we think are the essential types of production costs.
Average Cost
The average cost is determined by the total cost of one unit in your production line. You can calculate the average cost by figuring out the total cost of production and then dividing that sum by the number of units you produce. If it costs $100 to produce 100 widgets, then the average cost is $1.
Fixed Costs
Fixed costs, as the name implies, are costs that don’t change over time. Fixed costs aren’t influenced by the amount you produce when in production, but are still part of the overall cost of production. Even if you’re not in production planning, a company is still responsible for paying fixed costs. These costs include rent for the facility or factory in which you manufacture products, salaries, utility bills, insurance, loan repayments, etc.
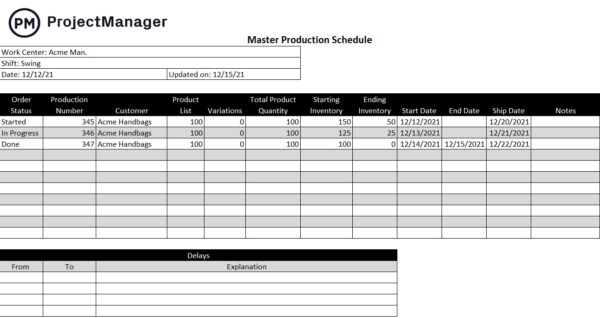
Variable Costs
Variable costs are costs that change and are wedded to the production process. Over time, these costs can fluctuate, making them harder to accurately forecast. If production sales go up, variable costs will do the same. If production costs go down, then so do the variable costs. Examples of variable costs in manufacturing are the cost of raw materials, piece-rate work, production supplies, commissions, delivery costs, packaging, credit card fees, etc.
Direct Costs
As noted, direct costs are tied to the production process of your product line. Direct costs tend to be variable costs, but not always. They can also be fixed costs. The rent for a factory is tied to production and, therefore, part of a company’s direct costs. Other direct costs are manufacturing supplies, equipment, raw materials, labor costs and whatever other production costs are tied to the making of the product.
Indirect Costs
We briefly defined indirect costs as those production costs that aren’t directly associated with the production of a product. These can be supplies, depreciation, utilities, production supervisory wages, machine maintenance and repair, fringe benefits of the indirect manufacturing personnel, etc. Indirect costs are sometimes referred to as factory overhead and manufacturing overhead.
Overhead Costs
Overhead costs make up the total of all the indirect costs that are incurred during the production of a product. Overhead costs are included in the cost of finished goods in inventory and work-in-progress inventory when looking at a manufacturer’s balance sheet. These costs include indirect labor, indirect materials, utilities, physical costs, financial costs, etc.
Marginal Costs
Marginal costs are those costs that come about due to a company producing additional goods because of accidental damages or other causes. These costs, however, don’t impact the fixed costs, but they can increase the variable cost.

Get your free
Capacity Planning Template
Use this free Capacity Planning Template for Excel to manage your projects better.
Production Costs Examples
To better understand what the cost of production is, let’s make up a fictitious manufacturer company, Steelco. They manufacture stainless steel furnishings for industrial and commercial food manufacturers. Let’s follow a job through the various production costs.
Labor Costs
To begin, let’s look at the labor costs involved in steel fabrication. Some designers come up with blueprints of what needs to be made. Then there are the fabricators who work the machines, cutting and welding the steel. Monitoring their work are floor managers who ensure that they’re doing everything to spec and quality standards are being met. This is, of course, a superficial look at the labor costs, but for our purposes, it illustrates the various jobs related to producing fabricated steel furnishings.
Related: 10 Free Manufacturing Excel Templates
Material Costs
The company could buy steel or fabricate it. If they’re making steel, then they’ll need raw materials such as iron ore, coal and scrap steel. These materials are mixed and made into steel in a blast furnace. The cost of these materials, whether it’s fabricated steel that’ll be made into the restaurant furnishings or the raw materials to make the steel are all part of the cost of production.
Maintenance Costs
There’s a lot of equipment used in fabricating metal. A short list includes press breaks, plate rolls, angle rolls, band saws, ironworker machines, metal shearing machines, laser cutting machines, weld positioning, plasma cutting machines, milling machines, punch press, metalworking lathes and more. All of these machines need maintenance to ensure they’re running properly and that there aren’t delays. There will also be regular repairs and occasional replacements. All of these costs must be collected.
Once there’s a list of all the costs associated with the steel fabrication, Steelco would have to add it up and then divide that figure by the units produced to determine the production cost.
How to Track Production Costs With ProjectManager
That’s a lot of costs to keep track of on top of managing your production line. To track all those resources so that you stay productive and deliver quality products without going over budget you need project management software. ProjectManager is online project management software that monitors resources in real time to help you manage costs. That means you can catch issues quickly and get back into production fast without wasting money that will cut into your profits. Here are some tools that monitor your production costs.
Use Secure Timesheets
Labor costs are an important part of overall production costs. Being able to track those costs securely helps ensure that you don’t go over budget. Our timesheets update automatically as hours as logged through the software. You can add tasks from different production projects, copy timesheets from week to week if there aren’t any changes and even auto-fill timesheets. Once timesheets are submitted, they’re locked and cannot change. Plus, timesheets won’t be routed to payroll until an administrator has looked them over and they’ve been approved.

Keep Track of Your Team’s Workload
Your most valuable resource is your production team. They work the production line and make products. If you aren’t productive, production costs will go up. But if you over-task them, you’ll have delays and erode morale. That’s only going to lead to further production costs. We have resource management features that ensure your production teams are working at capacity. For example, our workload chart is color-coded so it’s easy to see who has too much work and who has too few jobs. You can reallocate resources right from the workload chart and stay productive, on schedule and within budget.
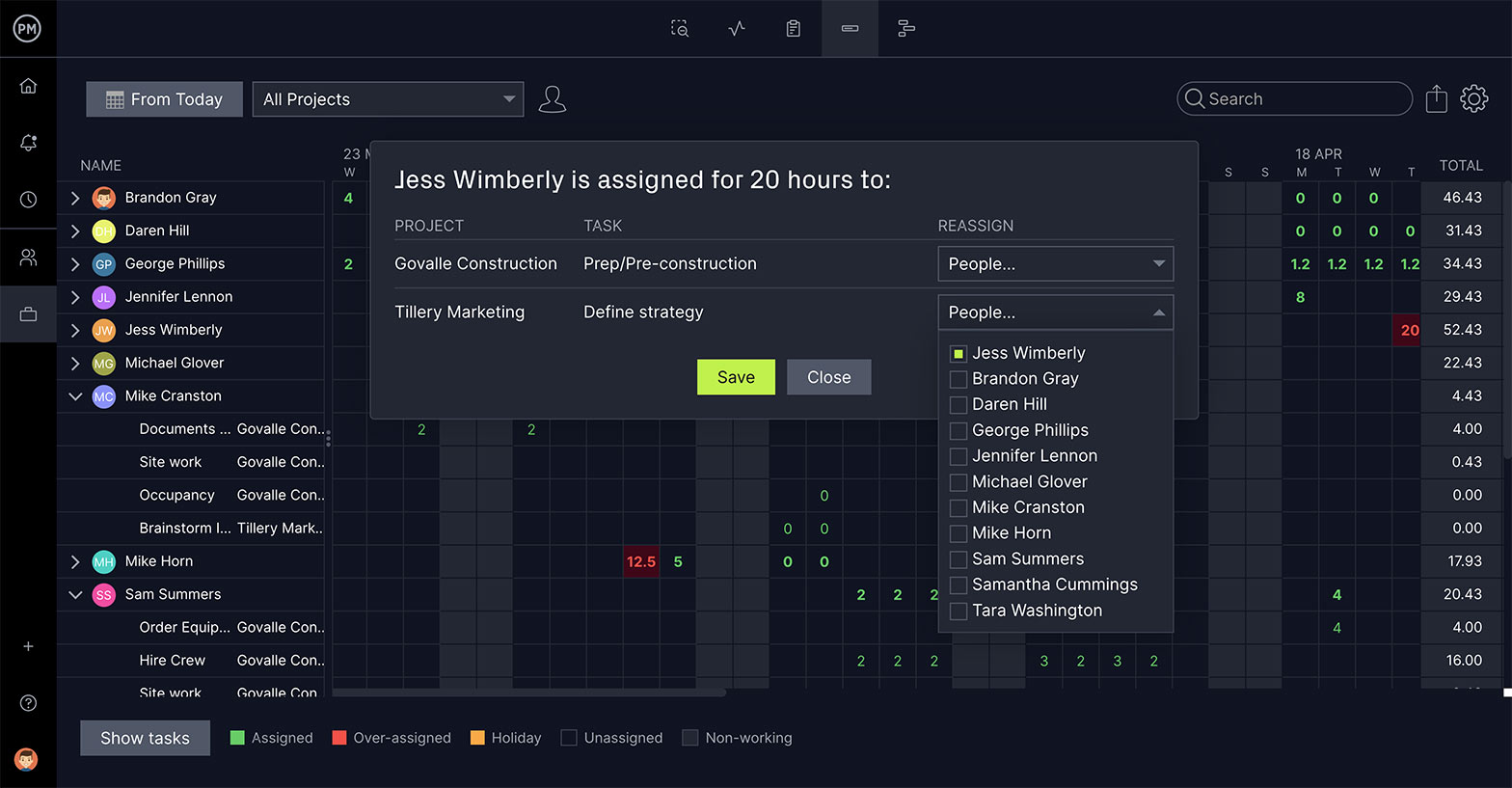
There are other tools that can help you track cost of production. Get a high-level view of costs and other metrics with our real-time dashboard. It automatically collects data, which is displayed in easy-to-read graphs and charts. There’s no time-consuming setup, either, as with lightweight tools. It’s plug–and–play. For more detail, use our customizable reports. You can generate reports on costs, timesheets, workload and more and they’re easy to share with stakeholders to keep them updated.
ProjectManager is award-winning project management software that helps you plan, manage and track your production costs in real time. Automate workflows to streamline production and set up task approvals to ensure that only quality moves through your production line. Get started with ProjectManager today for free.