The better a business’ warehouse operations, the more successful the business is. Warehouse management ensures that stock matches customer demand. Warehouse operations take into account the supply chain and work towards being cost-effective and efficient.
To understand effective warehouse operations, you must first be clear on the warehouse operations process and how it plays into the larger warehouse operations management. Read about that and how to improve the efficiency of warehouse operations.
What Are Warehouse Operations?
Warehouse operations consist of the processes used when managing the activities associated with receiving, storing, packing and distributing goods in a company’s stockroom. This includes warehouse management systems (WMS), workflow processes, human and nonhuman resource management and more.
Warehouse operations aim to satisfy customer needs and requirements while optimizing space, equipment and labor as effectively as possible. That means that stored goods must be accessible and protected from damage. Achieving these goals requires ongoing planning and being able to quickly adapt to change.
Project management software can help manage the warehouse operations process to reach its objectives. ProjectManager is award-winning project and portfolio management software with powerful kanban boards that help control the inventory life cycle. Kanban boards can be set up to reflect the warehouse operations process, while kanban cards can capture data from individual orders. Each card can track planned versus actual progress, schedule resources and more to keep warehouse operations running smoothly. Get started with ProjectManager today for free.
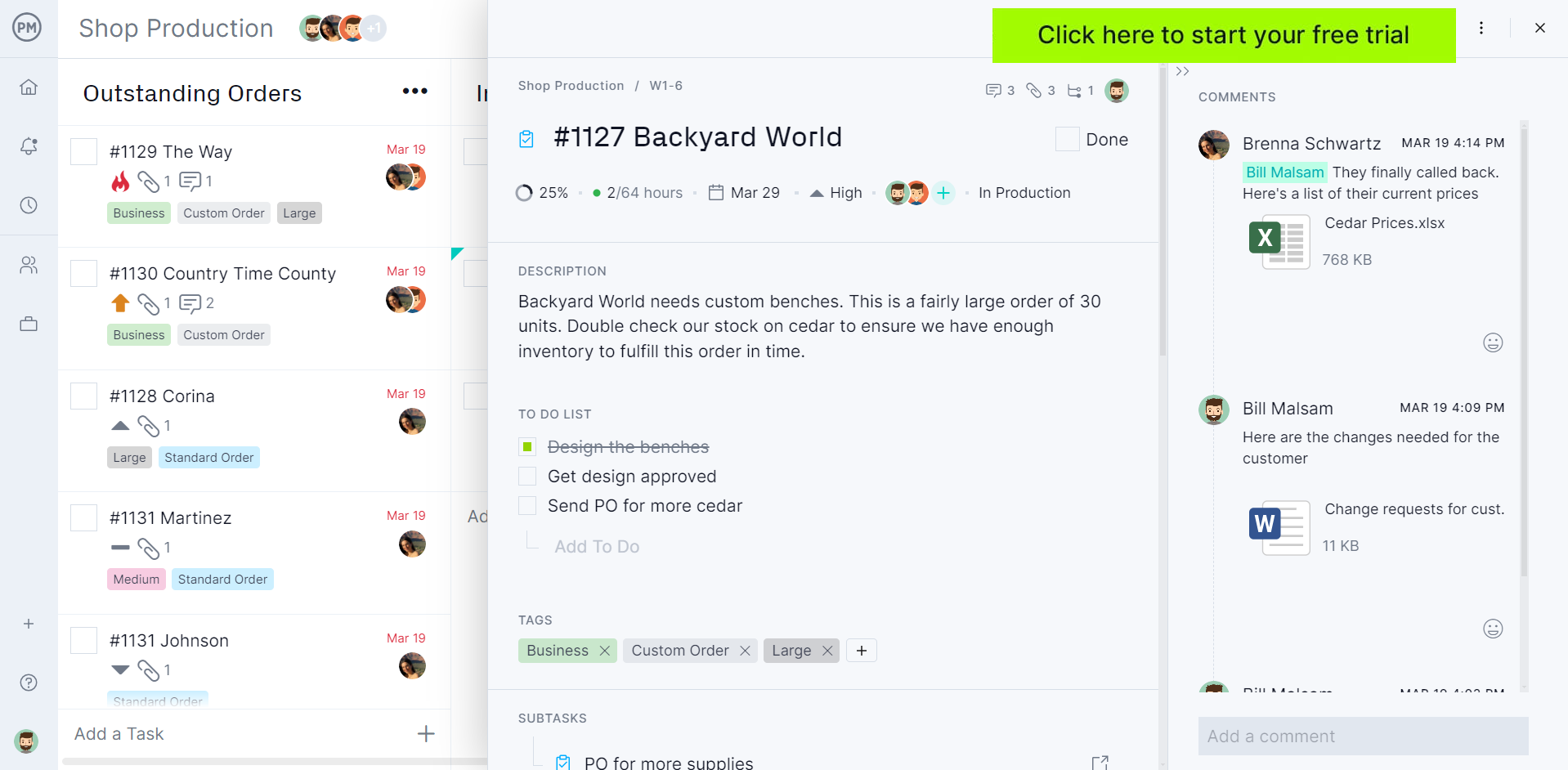
The Warehouse Operations Process
Project management software will help control the warehouse operations process. However, this requires an intimate understanding of the warehouse operations process. There are six fundamental processes to warehouse operations: receiving, storing, picking, packing, shipping and returning. Being able to optimize these seven processes streamlines warehouse operations and reduces costs and errors, which leads to a higher perfect order rate.
Receiving
This is the first warehouse operations process, also one of the most important to perform properly. It starts by verifying that the right product in the right quantity and without damage was delivered. The responsibility of the goods is then transferred to the responsibility of the warehouse, which is now tasked with maintaining the condition of the goods as received until shipped. Doing this allows warehouses to filter out damaged goods and avoid liability.
Put-Away
Once received, the goods must be taken from the receiving dock to their warehouse storage location. Not putting goods in their proper place interferes with warehouse operations and reduces productivity. Putting away goods also allows them to be stored more efficiently, reduces travel time, ensures safety for goods and employees, utilizes space better and makes it easier to find, track and retrieve when needed.
Storing
This leads to the next warehouse operations process, storing the goods. Put-away moves the goods from where they’re received to the warehouse. Storing is finding the opportune site to store each of the goods that are received. As noted, this helps optimize space and increase labor efficiency.
Picking
When a customer order comes in, goods must be retrieved, which is the picking process in warehouse operations. This is the most expensive process in warehouse operations and can be over half of the total operating expense for the warehouse. Therefore, being as efficient as possible with the picking process can save money and increase warehouse efficiency. Another advantage of streamlining the picking process is it increases accuracy as errors negatively impact customer satisfaction.
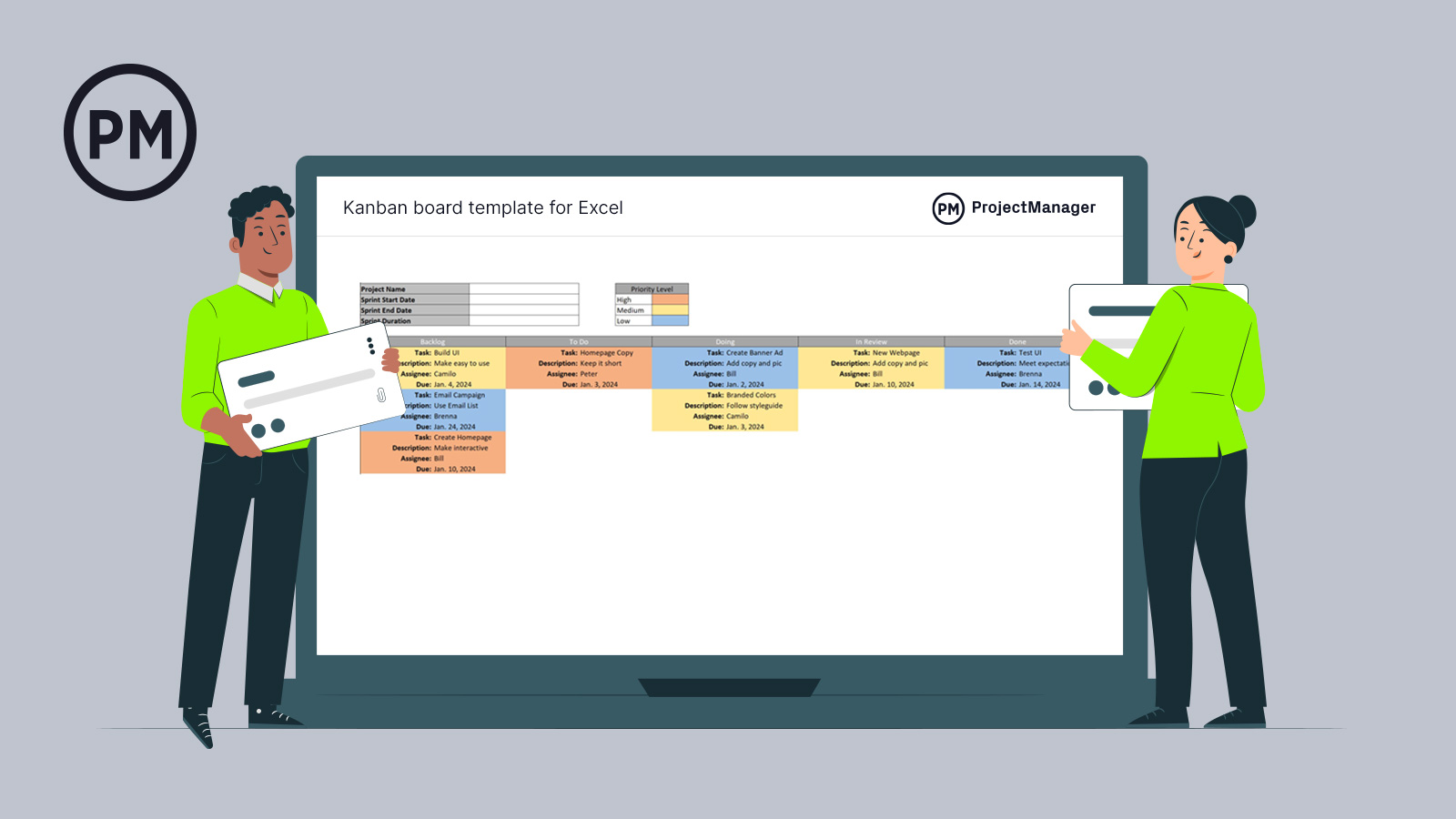
Get your free
Kanban Board Template
Use this free Kanban Board Template for Excel to manage your projects better.
Packing
Once picked, the goods must be packaged. Packing is the consolidation of picked goods from the customer’s sales order that’s then prepared for shipment, such as putting them in boxes and adding address labels. It’s important to avoid damages during this process and when packing use lightweight materials that protect the goods but don’t add undue costs to shipping.
Shipping
The final step in the warehouse operations process is shipping (unless goods are returned, but we’ll get to that in a moment). If all the other processes have been done correctly, all that’s needed is to ensure that the package is delivered to the right address and customer when it’s expected and without damage. Also, shipping should be as economical as possible for the shipper without impacting the delivery for the customer.
Returning
Occasionally, goods will be returned due to damage or an error. This process begins with the prior process. When shipping, a return label should be included in the packaging. Once the return is delivered to the warehouse, staff should inspect it for damage, review the reasons for its return and scan it back into the tracking system. If the item isn’t damaged or expired, it can be returned to its place in the warehouse, otherwise, it should be discarded or salvaged. Detailed records of this process should be kept.
What Is Warehouse Operations Management?
Warehouse operations management is simply the principles and processes involved in running the day-to-day operations of a warehouse. This includes all processes defined above, but also the scheduling of labor and the management of inventory and order fulfillment. Warehouse operations management seeks to have all these aspects of running a warehouse’s operations work together as efficiently as possible to increase productivity and reduce costs.
How to Improve the Efficiency of Warehouse Operations
It’s clear that improving the efficiency of warehouse operations is key to running a successful business, but what are some practical things that can be done to increase efficiency? Below are some of the things that warehouse operations will benefit from employing.
Use a Warehouse Management System
A warehouse management system is made to increase efficiency and accuracy in the warehouse operations processes. The software can be found in businesses working in retail space, distribution and manufacturing. That’s because the WMS improves the flow of goods through automation, which eliminates human error, reduces labor costs and can track orders.
Automate or Outsource Warehouse Operations
Automated workflows will help streamline warehouse operations processes, but businesses can also remove the entire process by partnering with a third-party vendor. This provides companies with a more experienced and likely better service at a lower risk to them. It can also reduce costs, help with compliance with current guidelines and keep organizations focused on their core strengths.
Use Kanban Pull System for Inventory Management
Kanban pull system is ideally suited for warehouse operations because of its lean approach similar to just-in-time stock control. It means that work starts only when the customer submits a purchase order. This is a visual workflow tool designed to reduce waste, minimize inventory levels to just what’s needed at the moment and improve inventory control. This leads to cost savings and greater efficiency and the dividends are more customer satisfaction.
Optimize the Warehouse Layout
The better a warehouse is laid out, the more streamlined its processes. The benefits include less time wasted having to retrieve or pick goods, quicker turnaround times and it gives a warehouse capacity to handle a larger volume of orders. All this leads to greater customer satisfaction as well as loyalty, as they appreciate getting orders on time and in good condition.
Implement Lean Manufacturing Principles and Techniques
Lean manufacturing is all about reducing waste and increasing productivity and customer satisfaction. Running a lead warehouse does all that by taking advantage of opportunities for improvement and focusing on value creation for customers. It streamlines warehouse operations processes. It’s based on the lean manufacturing principles of eliminating waste, reducing inventory levels and improving operational efficiency.
Warehouse Operations Roles and Responsibilities
Many warehouse professionals manage and run the warehouse operations processes. Each has a distinct role and responsibility, which together keeps the warehouse operating efficiently. The following are the three basic categories of people who ensure the warehouse is working as it should.
- Warehouse Operations Manager: Oversees all daily activities of the warehouse. As part of the supply chain, they must be adaptable, open-minded, have strong communication skills and build and manage a self-sufficient team.
- Warehouse Supervisor: Also oversees the general operations of the warehouse and its staff, including recording and maintaining inventory, advising receiving and shipping as well providing training. They work under the warehouse operations manager.
- Warehouse Workers: The team responsible for managing customer orders, overseeing and processing incoming stock, picking, packing and shipping orders as well as dealing with returns.
Why Are Warehouse Operations Important for Businesses?
As stated at the start, a company involved in selling goods lives and dies by the success or failure of its warehouse operations. It’s that important for business. It satisfies customer demand and builds customer loyalty. Effective warehouse operations will increase productivity and much more. Here’s a short list.
Order Fulfillment Process
The order fulfillment process starts with receiving a customer’s order and ends with delivering the goods to that customer. Along the way, goods are stored and managed to avoid overstocking and shortages. Warehouse operations play a critical role in this process, ensuring that orders are accurately picked, packed and prepared for shipping.
Supply Chain and Logistics Management
The warehouse is a bridge between production and distribution in the supply chain. Warehouses store goods after they’re produced or procured until they’re shipped to the customer. That shipping is where logistics management comes into play. It ensures that goods are delivered to the right place, on time and in proper condition, while keeping costs low and maximizing efficiency.
Inventory Management
A warehouse serves to store inventory, which is why inventory management is forever tied to warehouse operations. That’s because inventory management controls the warehouse operations process from order to storing and selling of goods. It manages supplies and the floor of raw materials from procurement to finished products in production.
Operational and Production Costs
Without managing warehouse operations, costs are likely to get out of control. Operation costs include the cost of the goods being made and stored, but also all operating expenses, called selling, general and administrative (SG&A) expenses. Production costs are direct and indirect costs from manufacturing a product, such as labor, raw materials, etc.
How ProjectManager Helps With Warehouse Operations Management
Considering the importance of warehouse operations, businesses seek the best software to help them manage the warehouse operations process. ProjectManager is award-winning project and portfolio management software with the features to plan, schedule and track warehouse operations activities in real time. Resource management tools and cost-tracking features ensure that warehouse operations stay within budget and customers receive their orders on time.
Plan, Schedule and Track Warehouse Operations Activities
Warehouse operations include activities such as receiving, storing, packing and shipping, to name only a few. Planning out those activities on a robust Gantt chart makes sure that all those tasks are organized and assigned. Managers can see the whole plan in one place but also link all four types of task dependencies to avoid delays. When the schedule is complete, set a baseline to capture it and associated costs. This allows managers to track the planned effort against the actual effort in real time to stay on schedule.

Manage Resources and Monitor the Costs of Warehouse Operations
To keep to that schedule requires constant monitoring. Human resources are responsible for the day-to-day warehouse operations and their tasks can be viewed in one place on the team page or color-coded workload chart. If someone is over- or underallocated, balance their workload to keep everyone working at capacity. For a high-level overview, toggle to the real-time dashboard, with easy-to-read graphs and charts showing time, costs, workload and more.
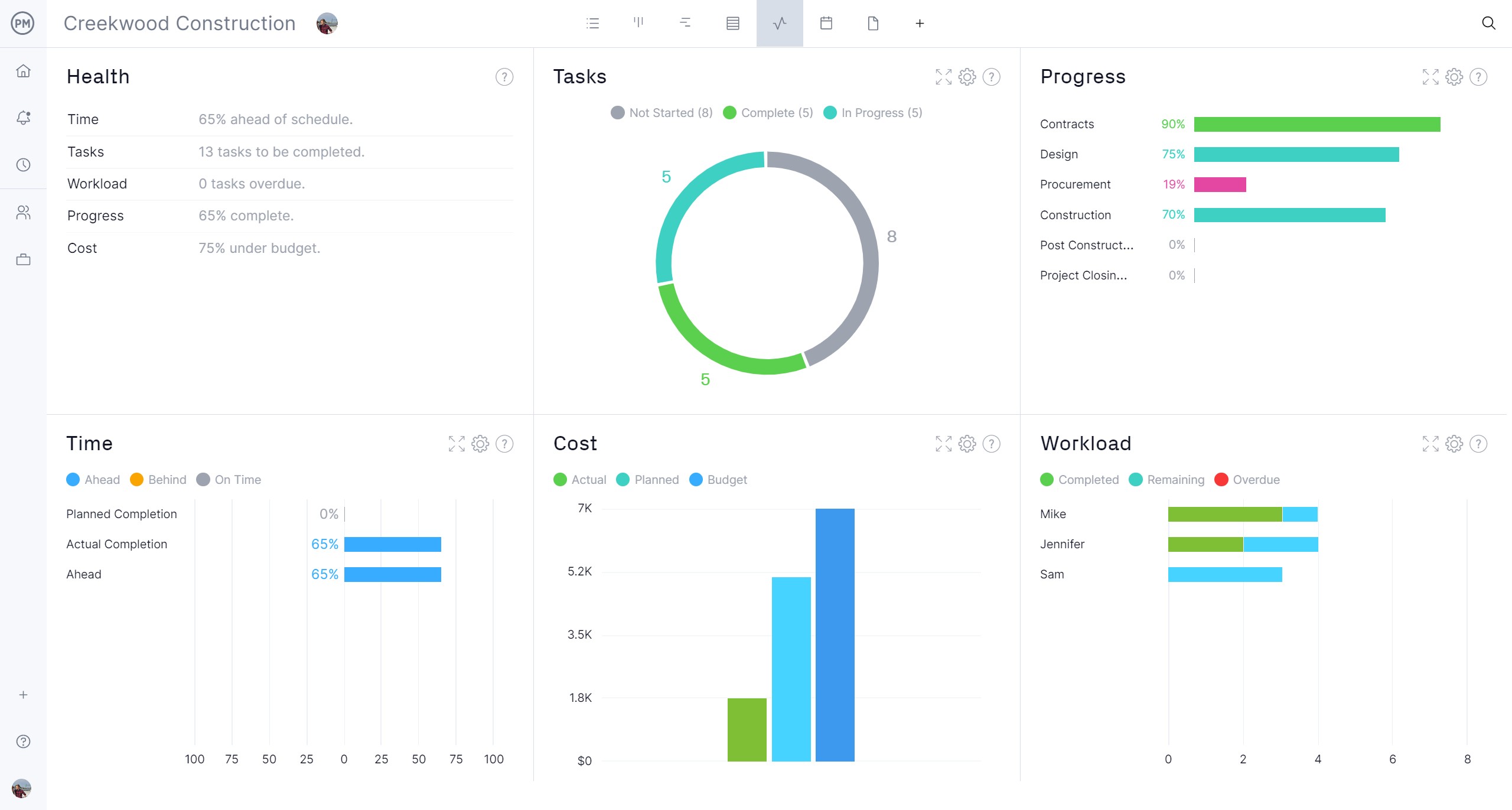
When more detail is called for, use the customizable reporting features. Reports on timesheets, project or portfolio status, variance, workload and more can be generated with a keystroke. All reports can be filtered to show only what’s important and then shared in a variety of formats with stakeholders to keep them updated.
ProjectManager is online project and portfolio management software that connects teams whether they’re in the office, in the factory or warehouse floor. They can share files, comment at the task level and stay up to date with email and in-app notifications. Join teams at Avis, Nestle and Siemens who use our software to deliver success. Get started with ProjectManager today for free.